Contrary to folk tales, driver detention fees aren’t a cash cow for trucking companies, owner-operators, or even the more reputable 3PLs.
It’s easy to see how shippers and facilities could make this mistake. Overseas container shipping companies are sometimes accused of unfair business practices for the ways they charge detention and demurrage. But it’s a different situation for domestic carriers.
Trucking companies charge these fees to mitigate risk. They are basically transferring a portion of the financial risk of delays and complications onto their partners. In fact, it might be even more accurate to say they charge them to incentivize facilities to turn their trucks around faster.
Driver detention isn't an isolated issue. Delays feed into a cycle of unpredictability that affects labor management, strains regulatory compliance, and adds complexity to an already volatile market.
Ultimately, the path to mitigating these challenges lies in mutual accountability and smart, data-driven strategies. It's about creating an environment where everyone, from drivers to facility managers, knows what to expect and can plan accordingly.
Truck Waiting Charges Can Sneak Up On You
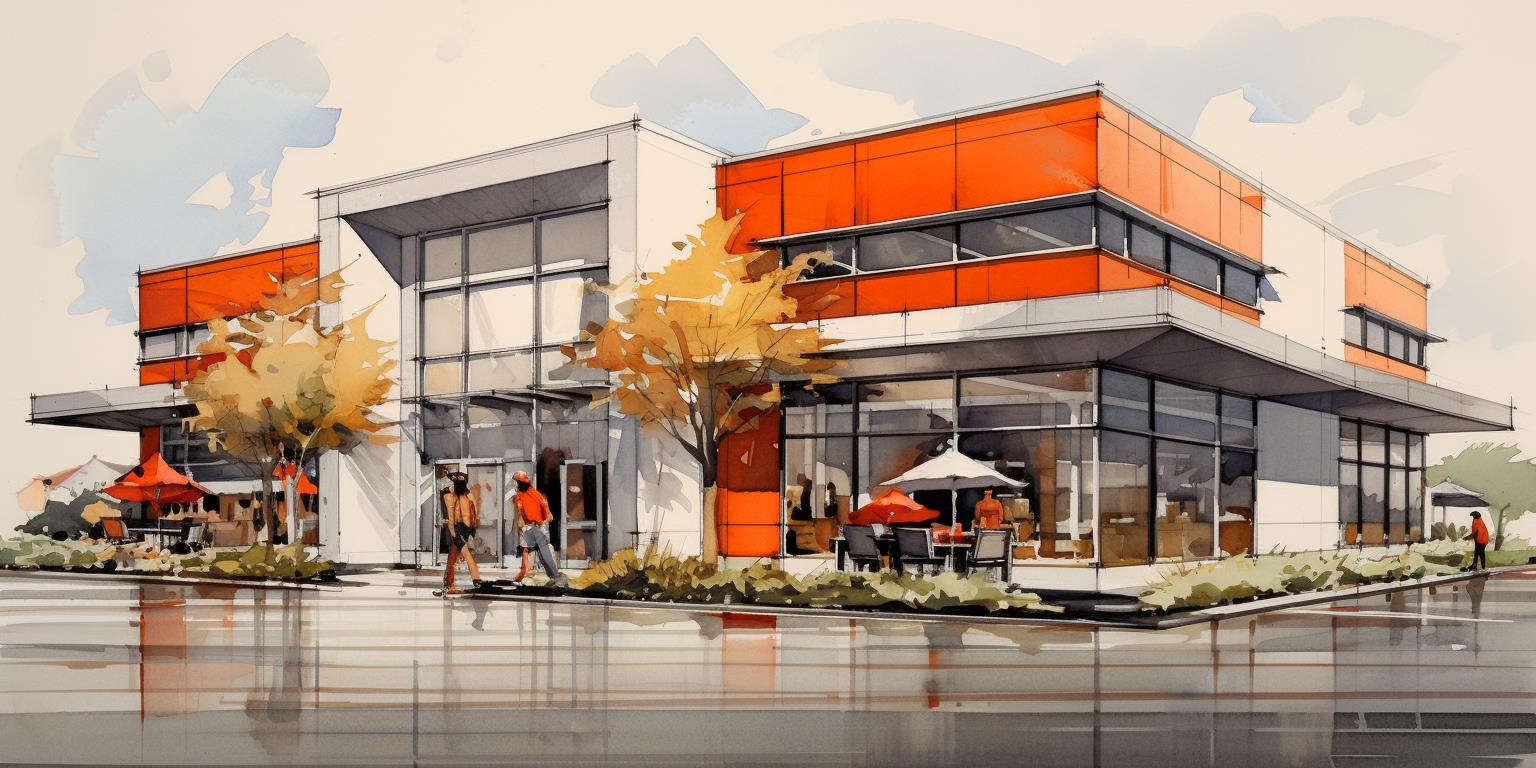
Detention charges might not seem like a life-or-death financial problem for your business. But when you don’t have a strategy to manage truck detention, the risk can escalate quicker than you might anticipate.
In April 2023, the retail giant Bed Bath & Beyond filed for bankruptcy. Court documents revealed that unpaid supplier invoices played a pivotal role in their spiraling debt crisis. Astoundingly, credit from logistics partners represented over a third of this category.
Now under new ownership by overstock.com, the brand has pivoted to an online-only model. In the aftermath of their financial turmoil, the company has taken legal action against two of their container shipping partners over alleged unreasonable detention and demurrage charges.
These kinds of lawsuits have been getting more and more common, but what you almost never hear about is a shipper or facility suing a trucking company over their detention fees.
The fragmented nature of detention charges, particularly when stemming from many smaller providers, often catches businesses off guard. These costs tend to get lost in financial reports, decentralized, and overlooked.
Carriers would rather build robust, long-term partnerships than upset facilities by charging these fees. But the trucking market is its own tangled web of tight schedules and thin profit margins. Detention fees are a symptom of a larger issue that requires accountability and a data-driven approach to solve.
The Tight Labor Market & Driver Detention Pay
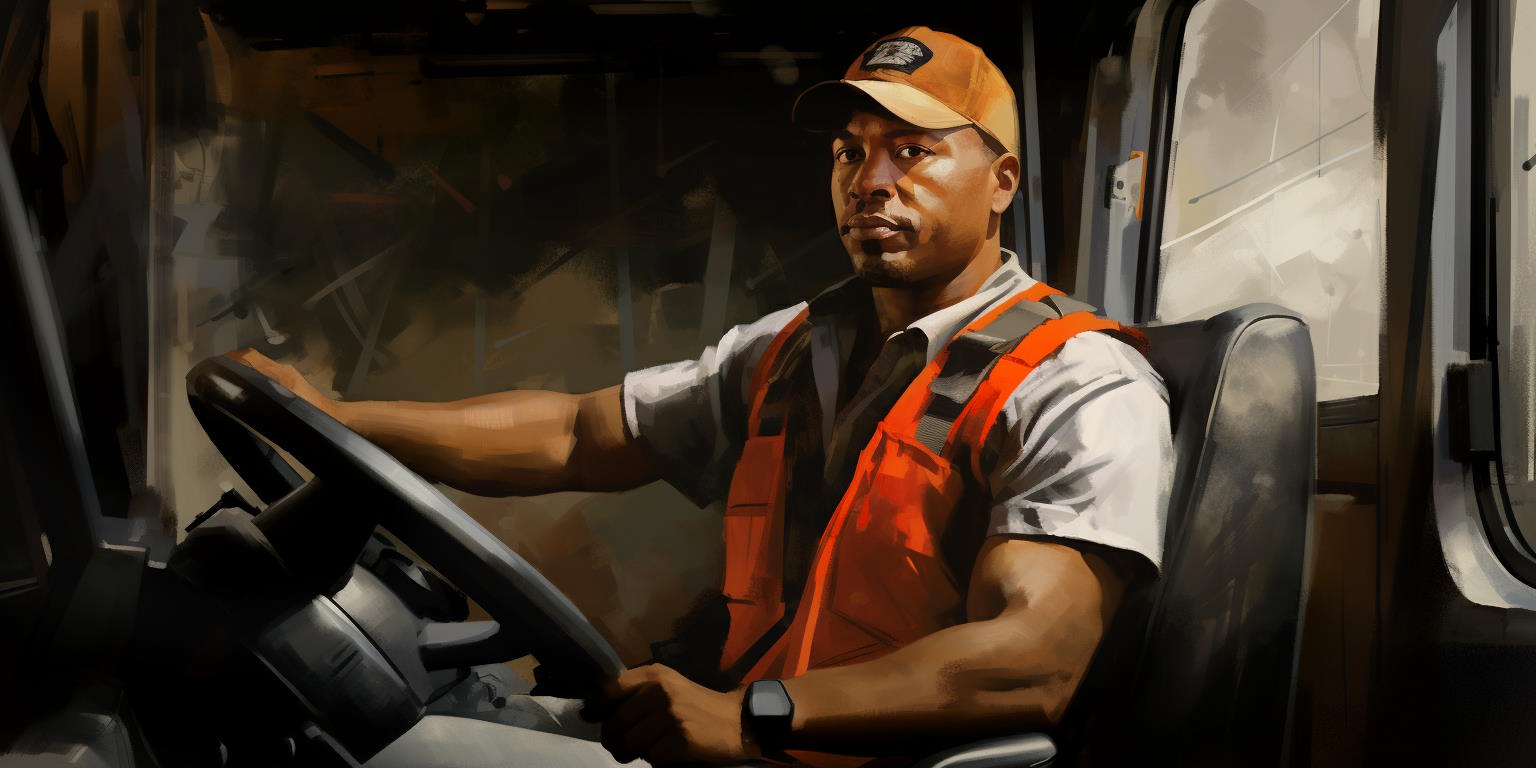
It's no secret that the U.S. is grappling with a truck driver shortage, causing ripple effects throughout supply chains.
But drivers are still typically compensated per mile, not by the hour. This model makes loading dock delays a significant issue. Some carriers are under pressure to transition to pay models that include hourly wages or even guaranteed weekly salaries.
The Federal Motor Carrier Safety Administration is also taking an interest, recently saying that uncompensated detention time is contributing to dangerous driving and “fixing” this issue is one of its highest priorities. This could lead to policy changes that incentivize or even mandate certain compensation structures.
For facilities, this means even higher detention fees could be on the horizon. And for the party that books the load, these costs might not even be visible - they could simply be factored into the overall prices charged by the carrier.
But facilities have an opportunity to take the initiative. Open, transparent conversations with carriers about loading dock efficiency can benefit everyone, including drivers. It's not just about reducing costs; it's about building a more efficient, less contentious supply chain that eases the strain of labor shortages.
Facilities can promise faster turnarounds for trucks that arrive closer to their scheduled time slots. In return, carriers could agree to reduce detention charges or even waive them when their trucks arrive late.
Dock scheduling provides the data that can make these conversations actionable, grounding everything in specific timings rather than assumptions and allowing for targeted strategies based on concrete metrics. This kind of two-way accountability could be the key to smoother operations and controlled costs.
When a Layover Fee Becomes the Facility’s Problem
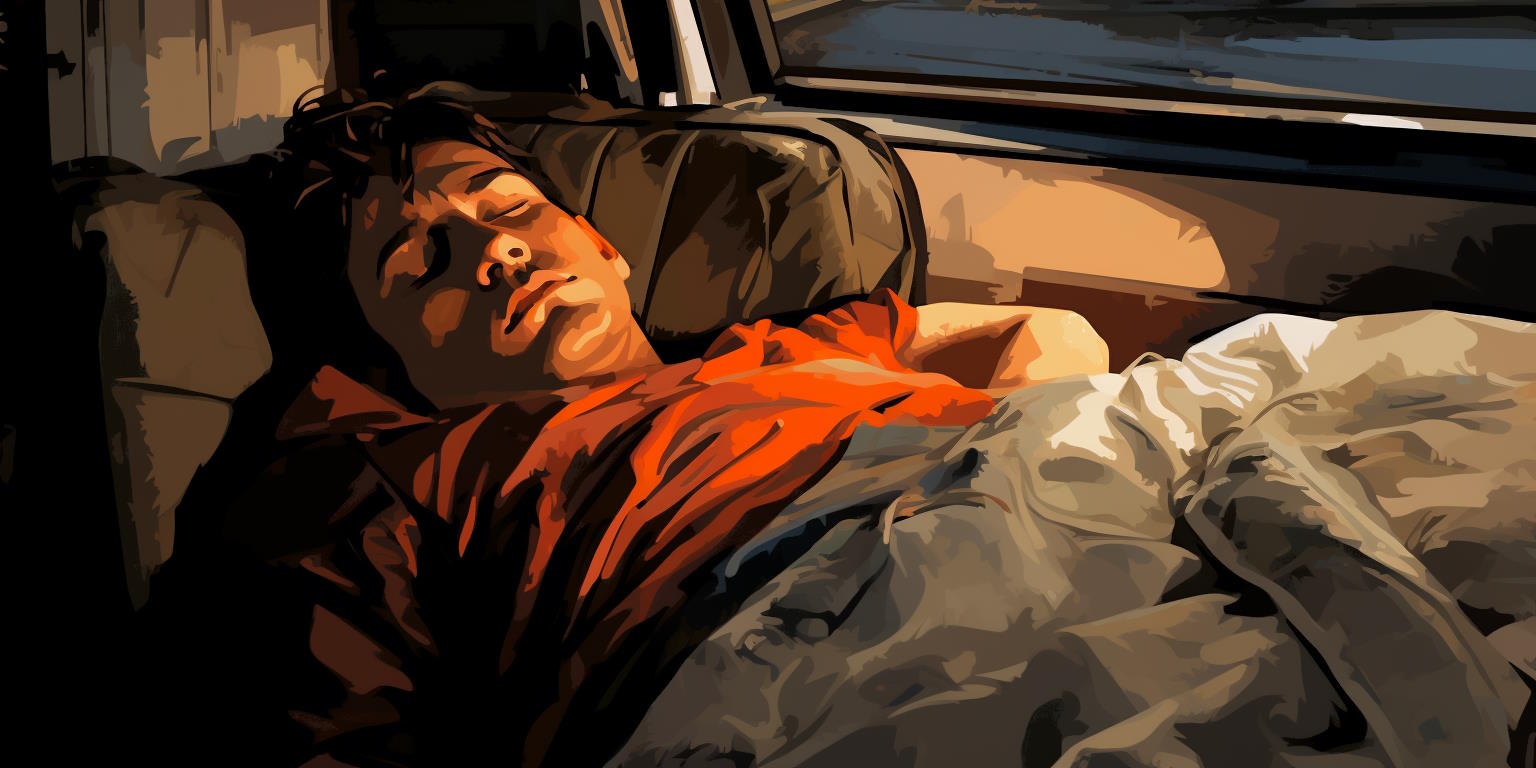
Overnight stops are a routine part of long-haul trucking, but when they’re unplanned — often a result of loading dock delays or scheduling mishaps — they introduce logistical headaches for carriers that they sometimes pass on to facilities in the form of even more costs.
According to U.S. Hours of Service regulations, drivers may drive up to 11 hours within a 14-hour workday, after which they are required to take 10 consecutive hours off duty. Exceeding these limits can be both unsafe and illegal, making proper planning crucial.
This complexity is one of the biggest reasons carriers can be hesitant to commit to strict timetables. For a dispatcher (or an owner-operator), the game is: how many miles can we fit in before the hours-of-service clock runs out?
Shortages in overnight parking represent another problem. While not always feasible, facilities with the space, security and legal framework may consider letting the first or last truck of the day stay on-site overnight. Not only does this make life easier for the driver, but may also provide some leverage in negotiations with carriers.
Above and beyond that, productive cooperation with carriers hinges on trust and performance. A facility that demonstrates its ability to turn trucks around quickly can lay the groundwork for more favorable terms. In essence, the message becomes, "You arrive on time, we'll expedite your load, and you can maximize your hours on the road."
Effective dock scheduling serves as both a tool for mutual benefit and a last-resort shield against liability for unplanned layovers. The right software not only provides concrete data for accountability but also streamlines operations for everyone involved.
Other Types of Accessorial Charges
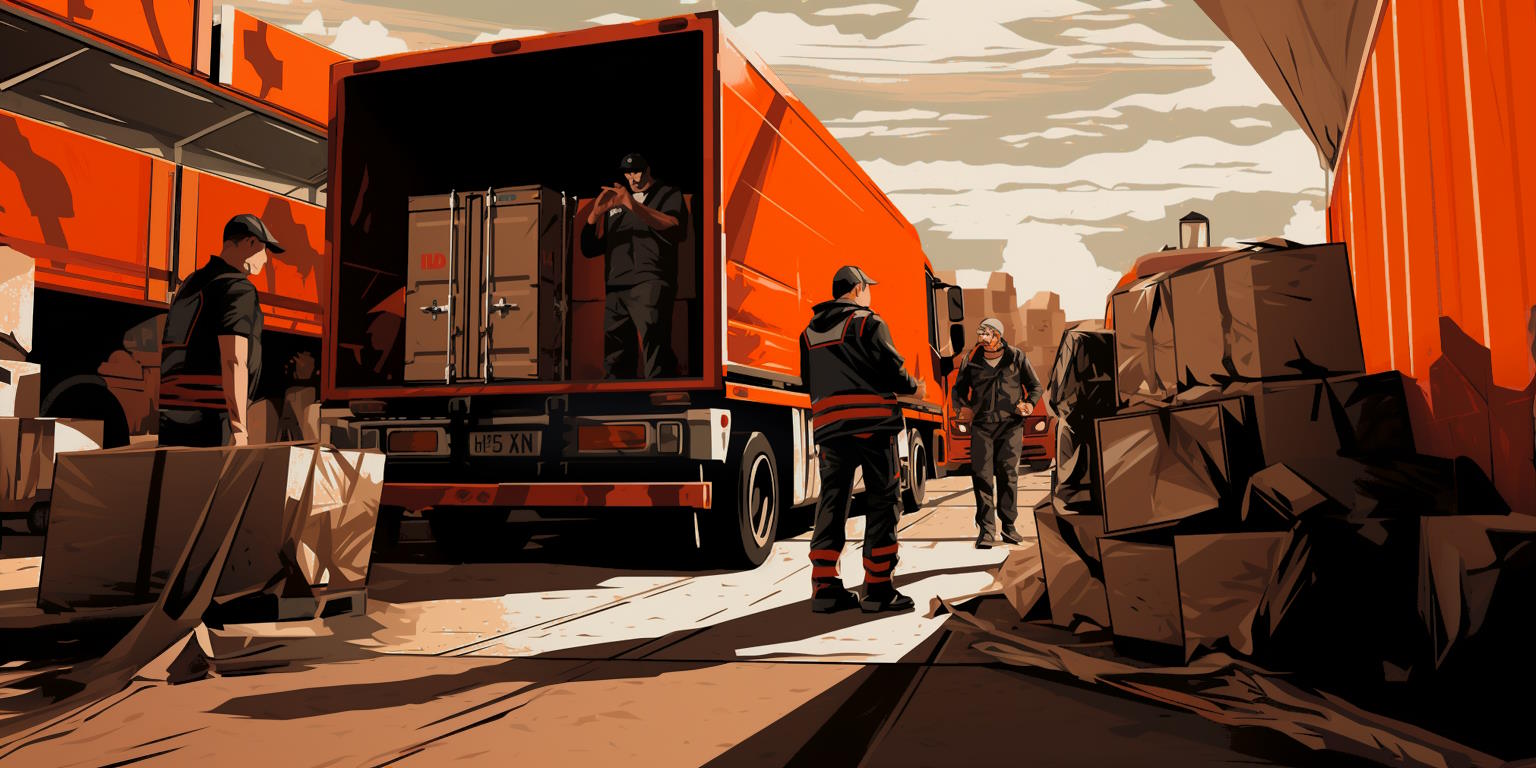
Detention fees sometimes fall under the broader category of accessorial charges. This is essentially a catch-all for additional costs that go beyond standard freight services, ensuring carriers are compensated for extra work and complexity.
They can range from the very specific, like needing a liftgate for delivery, to the more general, such as fees for navigating urban congestion. They serve as a monetary acknowledgement of the additional time, equipment, or risks involved that aren't part of a typical shipping contract.
While drivers once doubled as an extra pair of hands for unloading, health and safety concerns have largely shifted this role to specialized lumpers. Often contracted through the carrier, these services incur an extra charge, which can vary depending on the job's specifics. For example, LTL carriers sometimes require a lumper to avoid mixing up goods from different customers.
Accessorial charges are frequently levied for transporting goods requiring special care—such as perishable items, hazardous materials, or oversized loads. Similarly, they apply when the delivery location has unique requirements, like a narrow timeframe for delivery or limited dock space, complicating the carrier's job.
The costs involved in last-minute changes or cancellations are also sometimes listed as accessorial fees. The term has even evolved to include things like fuel surcharges. These developments signify a broader industry trend: carriers face increased volatility, even as technology makes some aspects of shipping easier and more cost-effective.
Having transparent discussions with carriers about what you can offer and need as a facility is crucial. It forms the basis for a mutually beneficial relationship and may open the door for innovative cost-saving measures for both parties.
The Domino Effect of Loading and Unloading Delays
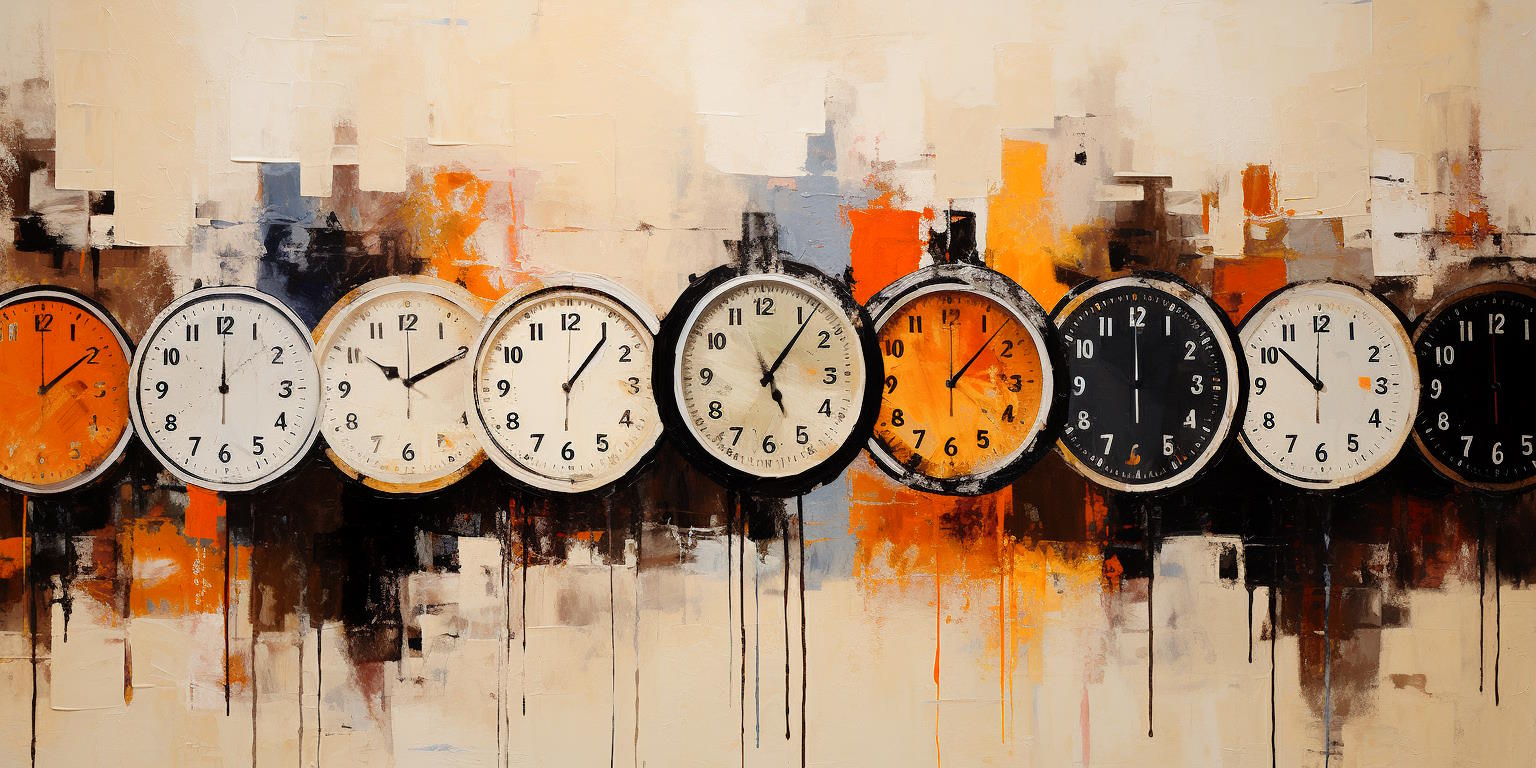
When it comes to logistics, time is a fragile variable.
One setback can easily snowball into a bigger mess that throws off everyone's schedule. And when the clock's ticking, money and patience start running thin.
Why do carriers charge detention fees? They're just handing the bill for that risk back to the facilities. The real question is, how do both sides work together to manage these delays?
Eliminating detention from contracts is an impractical solution in today's market. Similarly, a facility cannot expect to avoid these charges by only improving its internal operations.
The trick is finding the middle ground, a place where mutual accountability sets the stage for a no-nonsense agreement: "Show up closer to your scheduled time, and we'll get your truck worked faster. We'll even show you the data to back it up." This way, each side does its part to keep things moving, while fine-tuning their strategies and expectations.
Truck Dwell Time As an Accountability Measure
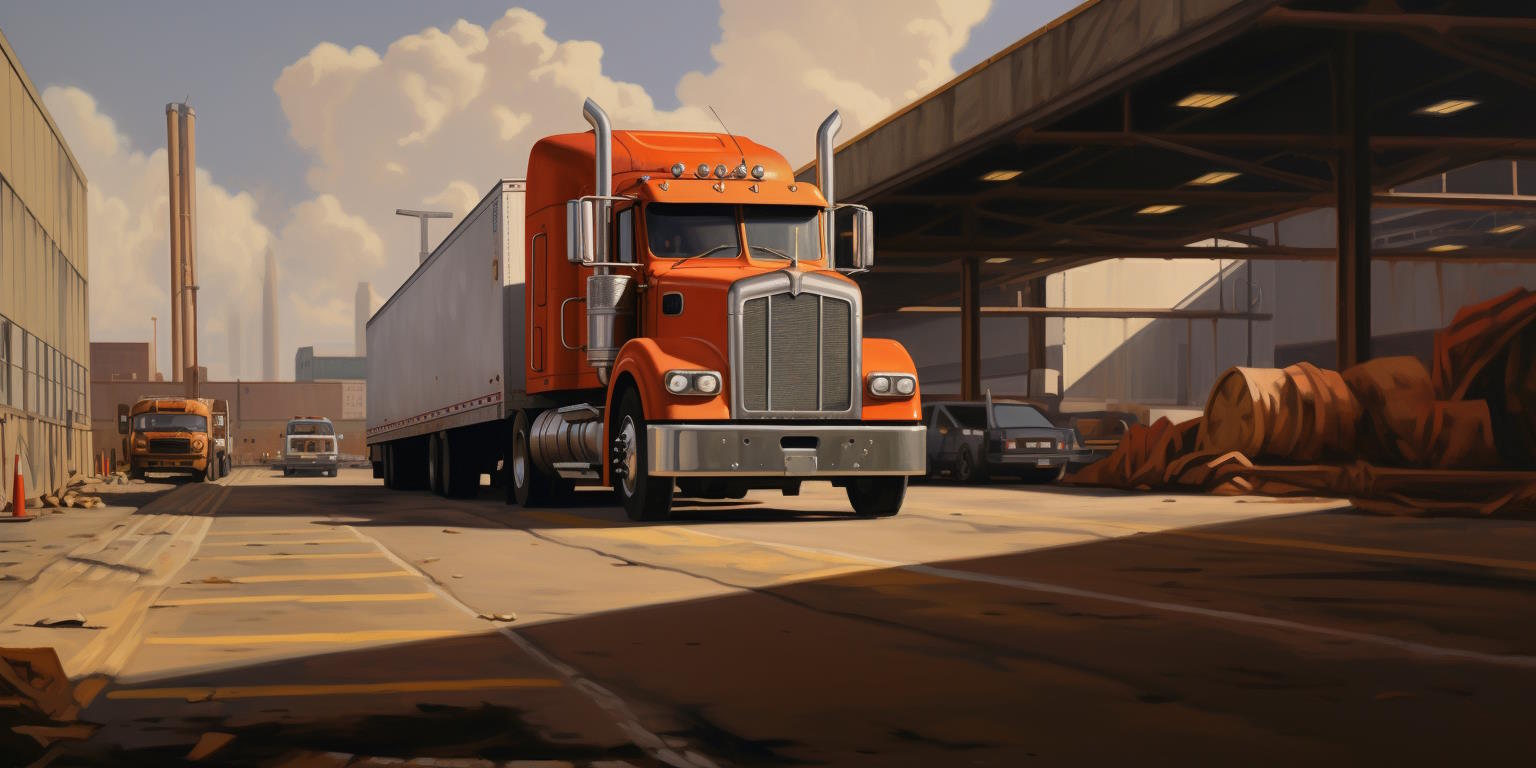
Accountability goes both ways. While carriers must do their part to adhere to schedules, facilities should also own up to their level of performance as well. Enter the metric of 'truck dwell time': the time it takes from a truck's arrival to its departure, a direct measure of how efficiently your facility is operating.
In other words, even if you have one carrier that waits just 90 minutes before charging detention, and another generous enough to give you 150, you ignore all that. You look at your average over a week and aim to cut it by 10 or 20 minutes. And you don’t stop until you’re turning trucks around in record time.
But you also want to look at dwell time alongside carrier performance. The idea is simple: the closer a carrier arrives to the agreed-upon time, the quicker they should expect to be on their way. You show them the data, week by week, that proves this point.
For example, last week a carrier was two hours late, and it took three hours to get their truck out of the facility. The week before, they were an hour late, and they were gone in under two hours. This week, they pulled in just 30 minutes behind schedule, and you had them rolling out in half an hour.
It's this kind of data that lays the groundwork for real discussions about efficiency and accountability. It lets you say, "Here's what happens when you're late, and here's how we do when you're on time."
DataDocks gathers the critical data that makes these conversations possible. Even the most skeptical carriers soon become enthusiastic once they experience the operational efficiency that smart dock scheduling unlocks.
To learn more about how DataDocks can help you get your detention fees under control and build mutual accountability with your carriers, give us a call on (+1) 647 848-8250, or book a demo.