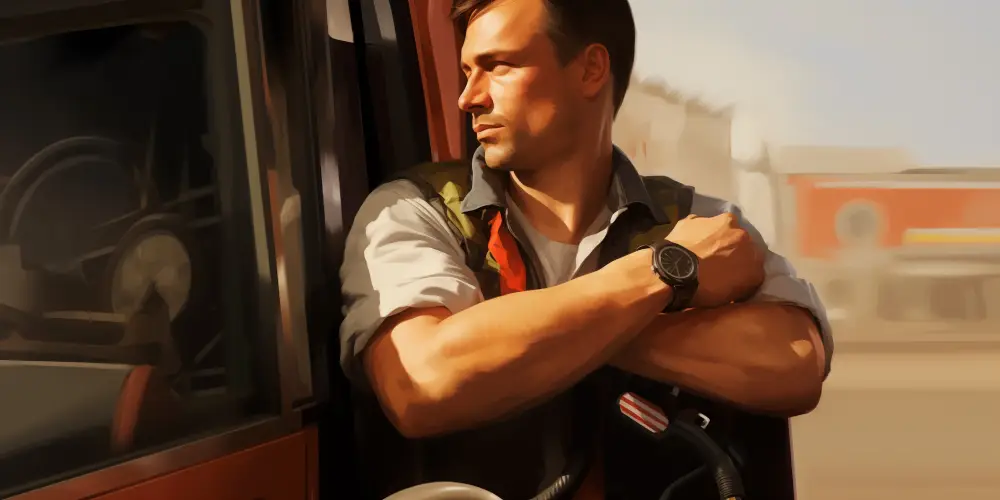
You're stuck at a busy loading dock, watching the clock tick away.
Your loads are going nowhere fast, and you're getting frustrated. This wait is what we call "dwell time."
But what is dwell time, and why should it matter to you?
It's more than just an inconvenience: it can lead to bottlenecks in production or fulfillment, and unexpected detention charges.
But here's the good news: dwell time doesn't have to be a constant headache.
In this guide, we'll clarify what dwell time is, why it's significant, and most importantly, how you can reduce it.
Let’s get started.
What Is Dwell Time In Logistics?
In logistics, dwell time refers to the time that a shipping vehicle (truck, boat, cargo plane, etc.) sits at the loading/unloading facilities(docks, ports, terminals, etc.)
There are four common types of dwell time throughout the supply chain:
- Cargo or container dwell time at terminals
- Last-mile vehicle dwell time in urban areas
- Vessel dwell time at ports
- Truck or trailer dwell time at loading docks
Let's break them down in simple terms.
Cargo or Container Dwell Time at Terminals
Cargo or container dwell time is the time that containers sit at ports or terminals, waiting to be loaded/unloaded onto ships, trains, or trucks.
Typical causes of delay:
- Customs clearance issues (e.g., inspections, incomplete paperwork).
- Congestion at the terminal, especially during peak shipping seasons.
- Carrier delays (trucks, trains, or ships arriving late).
- Labor shortages lead to slow loading/unloading.
Last-mile Vehicle Dwell Time in Urban Areas
The term "last-mile" refers to the final leg of a product's journey from a transportation hub (such as a warehouse, fulfillment center, or retail store) to its final destination—typically a customer's home or business.
Last-mile delivery faces more challenges in urban environments than in rural or suburban areas due to factors like:
- Traffic congestion: Urban centers have heavy traffic, which means delivery vehicles spend more time stuck on the road before even reaching their destination.
- Limited parking/loading zones: Unlike suburban areas where vehicles can park in driveways, urban environments have strict parking regulations and fewer dedicated loading zones. Delivery vans often have to circle the block searching for legal parking or are forced to double-park, which increases the risk of fines or towing.
- High delivery volume and density: Cities have a higher number of deliveries per square mile, meaning drivers must stop frequently. Each stop adds more dwell time because the driver has to find a legal place to park, unload packages, walk to the customer's address (sometimes several floors up in an apartment building), and get a signature or proof of delivery.
- Customer-related delays (e.g., no one available to receive the package).
Vessel Dwell Time at Ports
Vessel dwell time is the time a cargo ship (container ship, bulk carrier, or tanker) spends waiting at a port. This includes waiting for a berth, berthing, cargo loading/unloading, and un-berthing.
Typical causes of delay:
- Port congestion, especially during high-demand periods (e.g., holiday seasons).
- Berth availability – limited docking space at busy ports.
- Labor strikes or shortages slow down port operations.
- Adverse weather conditions prevent ships from docking.
- Port inefficiencies (e.g., outdated infrastructure, slow cranes).
Truck or Trailer Dwell Time at Loading Docks
This is the time a truck or trailer spends at a warehouse, distribution center, or retailer waiting to be loaded or unloaded.
It is often overlooked at the senior leadership level because it looks like such a ‘local’ problem—but carriers and warehouse managers know it has a huge impact and is super tricky to optimize.
Typical causes of delay:
- First-come, first-served scheduling leads to bottlenecks.
- Inefficient dock operations, such as slow unloading due to labor shortages.
- Poor communication between drivers and facility staff.
- Infrastructure issues, such as too few dock doors or a lack of equipment.
These dwell times can disrupt the flow of goods through your supply chain, lead to higher storage fees and demurrage charges (fees for containers staying beyond free time), and increase fuel costs due to prolonged waiting.
7 Root Causes of High Dwell Time at the Loading Dock
1. First-come-first-serve or inconsistent scheduling
The first-come-first-served (FCFS) basis becomes problematic because it prioritizes “order of arrival” instead of efficiency. So, if many vehicles arrive simultaneously, congestion builds up, making it hard to handle all the tasks at the loading dock.
Let’s say a warehouse receives 50 trucks per day. Without a proper appointment system, 30 of them might arrive between 8 AM and 10 AM, which makes it hard to keep up with all the trucks. Meanwhile, between 2 PM and 4 PM, only 5 trucks arrive, leaving docks idle for 4 hours.
Those 4 hours could’ve been utilized better with proper scheduling.
2. Lack of Visibility or Forecasting
If you still rely on outdated demand forecasting and lack real-time tracking, it’s almost impossible to prepare.
You won’t know when vehicles will arrive, and it’ll be hard to predict incoming shipment volumes. When you’re in this situation, you’ll have vehicles arriving too early or too late—causing either congestion or underutilized docks.
For example, if your warehouse expects 20 trucks on Tuesday, you assign enough dock workers for the 20 trucks. But if 40 trucks arrive due to miscommunication with suppliers, you won’t have enough dock workers, and unloading will be delayed.
3. Inefficient Check-in Procedures
If your check-in requires manual form-filling, it creates a backlog at the security gate, slows down the time it takes for vehicles to get assigned a dock, and extends dwell time.
Imagine you have a warehouse that receives 200 trucks per day. If each truck’s check-in takes 15 minutes due to paper forms, that’s 50 extra hours of dwell time per day.
There are also many cases of technical failures (e.g., RFID issues, barcode readers fail) that force fallback to slower, manual processes.
4. Lack of Alignment Between Check-In and Loading/Unloading Teams
Even if a vehicle arrives on time for its appointment, if your dock crew is still working on a previous load, it will have to wait before unloading can start.
This usually happens due to a lack of coordination and communication gaps between the loading and unloading teams.
So, make sure your warehouse teams communicate clearly to avoid situations like these and reduce dwell time.
5. Infrastructure and Equipment
Insufficient dock doors, poor warehouse layout, or outdated handling equipment will slow down the unloading/loading process.
If your warehouse has 10 dock doors but only 5 forklifts, unloading takes twice as long as it should.
But note here: many warehouses blame limited dock doors or outdated equipment for slow unloading—but often, the real issue is poor dock management. Separating the real problem from the typical excuse of “equipment constraint.”
6. Carrier Familiarity
New carriers take longer than regular carriers because they don’t know the warehouse layout, processes, or documentation requirements.
Drivers unfamiliar with the facility may take longer to park, check in, or locate the correct dock. In some cases, carriers don’t know warehouse rules, so they encounter documentation issues or miscommunication.
For example, regular carriers may complete unloading in 30 minutes, while new carriers could take 50 minutes due to process confusion.
However, a facility’s past dwell time is the strongest predictor of future dwell time performance. So, remember that refining your internal processes will affect your dwell time more than external factors like carrier familiarity.
7. Timing and Staffing
Understaffing during peak hours creates delays, while mismatched shifts lead to inefficiencies.
For example, if your warehouse operates from 9 AM to 5 PM, but 30% of trucks arrive after 6 PM, when staff is minimal, you’ll have trucks waiting overnight.
Some of the things you can do to prevent these are:
- Adjust staffing schedules to match peak vehicle arrival times.
- Offer flexible shifts or overtime to cover high-demand periods.
Use warehouse automation (robotic pallet movers, conveyor belts) to reduce reliance on human labor.
What Does Dwell Time Impact in Your Supply Chain?
Let’s dig into why dwell time is such a crucial factor in your supply chain.
Cost Implications
Extended dwell times come with a financial burden.
While your cargo waits, you're footing the bill for storage, maintenance, and labor. These costs can accumulate quickly and affect your profitability.
However, with shorter queue times and more predictable scheduling, your warehouse staff can complete tasks within normal shifts, lowering the need (and budget strain) for overtime hours.
Delivery Schedule Disruptions
Dwell time directly influences your delivery schedules.
For example, if you have shorter dock times, you can process more daily shipments without expanding your facilities. In optimized scenarios, you can even reduce the average truck queue from over 50 minutes to under 10.
But when goods don't move as planned, you risk missing delivery deadlines. This can result in dissatisfied customers and strained business relationships.
Detention Charges
Another consequence of dwell time is the potential for detention charges.
Detention fees are generally charged when the time for loading or unloading exceeds a pre-specified "free time," usually ranging from 1 to 2 hours. These charges compensate the carrier for the time the vehicle is held up, which could otherwise be used for transporting other goods.
If you reduce your dwell time, you can potentially cut yearly detention costs ($76,751 baseline) by 55–100% depending on the strategy (e.g., dispatching rules, automated check-in).
Resource Allocation
Inefficient management of dwell time can tie up your valuable resources.
Trucks, equipment, and personnel that sit idle could be used more effectively in other parts of your operation.
But that’s not all: dwell time can ripple through your entire supply chain.
Inventory Management
Prolonged dwell times can disrupt your inventory management. They can throw off cycle counts, limit your throughput, and pull labor away from picking and packing.
The more your system is clogged with goods in dwell, the less nimble your operations become.
This can lead to imbalances in your stock levels, potentially resulting in stock shortages or overstocking.
Customer Satisfaction
Your warehouse efficiency echoes through the demand chain, leading to higher customer satisfaction.
However, delivery delays caused by dwell time can leave your customers dissatisfied. Meeting customer expectations is vital for maintaining a positive reputation.
Operational Efficiency
Inefficiencies triggered by dwell time in one part of your supply chain can have a domino effect, causing a series of delays and disruptions.
However, utilizing your warehouse staff and system can lead to cost savings for your carriers, often resulting in greater reliability.
Sustainability & Compliance
If you have fewer roadside congestion and fewer bottlenecks, you’ll lower accident risks and regulatory headaches.
CO₂ emissions can also drop by up to 80% (baseline 219.13 tons/year) thanks to shorter wait times and smoother flows (Source: Science Direct). So overall, you have better sustainability, safety, & compliance.
Competitive Advantage
A supply chain that effectively manages dwell time gains a competitive edge. It can fulfill orders faster, control costs, and offer a better overall customer experience.
This, in turn, leads to you being able to be more efficient with every dollar you spend. You gain the power to outspend more of your competitors in key areas because you’re simply more streamlined than them.
How to Calculate Dwell Time
We know why dwell time is important to your supply chain. Now, it's time to get practical.
Let's break down the process of calculating average dwell times per time period, load type, or carrier.
Your main goal in calculating dwell time is collecting data.
You need to know:
- Exactly when each load arrived at your facility
- Exactly when it was either loaded onto or unloaded from the vehicle
- Exactly when it departed from your facility
Once you know that, some simple math will tell you what your dwell time was for that particular load. Just add up how long the truck or container waited before moving on to its next destination.
Then, do that for each load in a given month and take the average. That will leave you with your average dwell time.
Optimize this number, and you’ll gain insight into how efficiently your supply chain is working. This could save you a lot of headaches—and a lot of money.
Once you know the numbers, here are seven practical strategies to reduce dwell time and boost your supply chain's efficiency.
7 Actionable Strategies to Reduce Dwell Time In Logistics
1. Smarter Scheduling & Vehicle Prioritization
Efficient scheduling stops congestion before it starts.
- Time-slot arrivals — align truck ETAs with dock availability so vehicles don’t stack up.
- Real-time updates — use a live scheduling tool to reshuffle slots the moment a bay opens or a truck is delayed.
- Off-peak incentives — offer lower rates or faster turnarounds for night or weekend deliveries.
- Fast-lane rules — give on-time, quick-turn trucks a “priority” lane instead of first-come-first-served.
- Communicate the rules — send priority criteria to carriers ahead of time so drivers arrive prepared.
2. Digitize Documentation & Communication
Paper and phone trees slow everyone down.
- Electronic Bills of Lading and e-signatures cut manual data entry and typos.
- Auto-updated records keep yard staff, dispatchers, and finance on the same page.
- Instant-messaging portals push delay alerts to drivers and stakeholders the moment anything changes.
3. Leverage Real-Time Tech & Visibility
Know exactly where every trailer and pallet is—right now.
- GPS / telematics tracking for private fleets or dedicated carriers.
- Barcode or QR scans at check-in to remove clipboard bottlenecks.
- RFID tagging for hands-free identification—backed by a manual fallback plan.
- Live yard dashboards so dock managers can see stalls, inbounds, and dwell-time hot spots at a glance.
4. Cross-Train & Incentivize Your Team
People—not just systems—make dwell go down.
- Multi-skill crews: loaders who can run paperwork or operate yard jockeys when lines back up.
- Ongoing development keeps staff current on best practices and safety standards.
- Shared-gain incentives reward teams—and even carrier partners—when average dwell times fall below target thresholds.
5. Optimize Yard Flow & Pre-Staging
A well-orchestrated yard keeps docks free and trucks moving.
- Designated staging zones keep entrances and fire lanes clear.
- Call trucks only when a door is ready to avoid clogged aprons.
- Pre-stage outbound freight so drivers hook and roll.
- Cross-dock when possible to bypass storage altogether.
6. Introduce a Drop-Trailer Program
If yard space allows, switching certain lanes from live-unload to a drop-trailer model can slash detention fees and idle minutes. Drivers decouple and go, while your crew unloads on its own schedule, freeing doors for the next arrival.
Not sure which path fits your network? Read our guide to the trade-offs of drop trailers vs live unloading.
7. Monitor, Analyze & Improve Continuously
What gets measured gets shortened.
- Track average dwell per truck, percentage of loads exceeding target time, and dock turns per hour.
- Slice data by hour, carrier, lane, and product to spot chronic laggards.
- Hold weekly stand-ups to tackle recurring issues; model “what-ifs” before changing schedule blocks or yard layout.
- Treat every dwell-time save as a blueprint—then rinse, refine, repeat.
Implementing these seven strategies will keep trucks—and revenue—rolling instead of resting in your yard.
Reduce Your Dwell Time & Boost Your Supply Chain Efficiency
Dwell time can significantly impact your budget, delivery schedules, and stakeholder relationships. The longer your cargo sits idle, the higher the costs and the more disruptions you face.
But we're not just here to tell you about the problem—we're here to offer solutions. We've shared seven practical strategies to help you address dwell time effectively.
By implementing these strategies, you can start reducing dwell time and making your supply chain more efficient.
Now, it's your turn. Take the insights you've gained here and apply them. Review the strategies we've outlined and identify areas in your supply chain where you can improve.