Inside most modern warehouses the facility runs on scanners and dashboards. Yet just beyond the dock doors the yard can still feel like another era. Guards key trailer numbers into spreadsheets, supervisors need walkie-talkies, and drivers have to wait because no one is quite sure which door will free up next.
Those minutes cost labour, detention fees, and customer goodwill.
A yard management system (YMS) promises to cut that waste with live trailer visibility, task queues, and trustworthy data. But “yard” means completely different things in different industries: a regional 3PL turning mixed-pallet loads all day needs different tools from a chemical plant monitoring hazmat tankers. Features, ease of use, pricing, and vendor support vary just as widely.
This guide breaks down the eight leading YMS platforms. For each one we outline where it shines, where it struggles, and the type of operation it truly fits, so you can choose a system that solves today’s challenges and won’t hold you back in future.
8 Best Yard Management Software Options in 2025
DataDocks
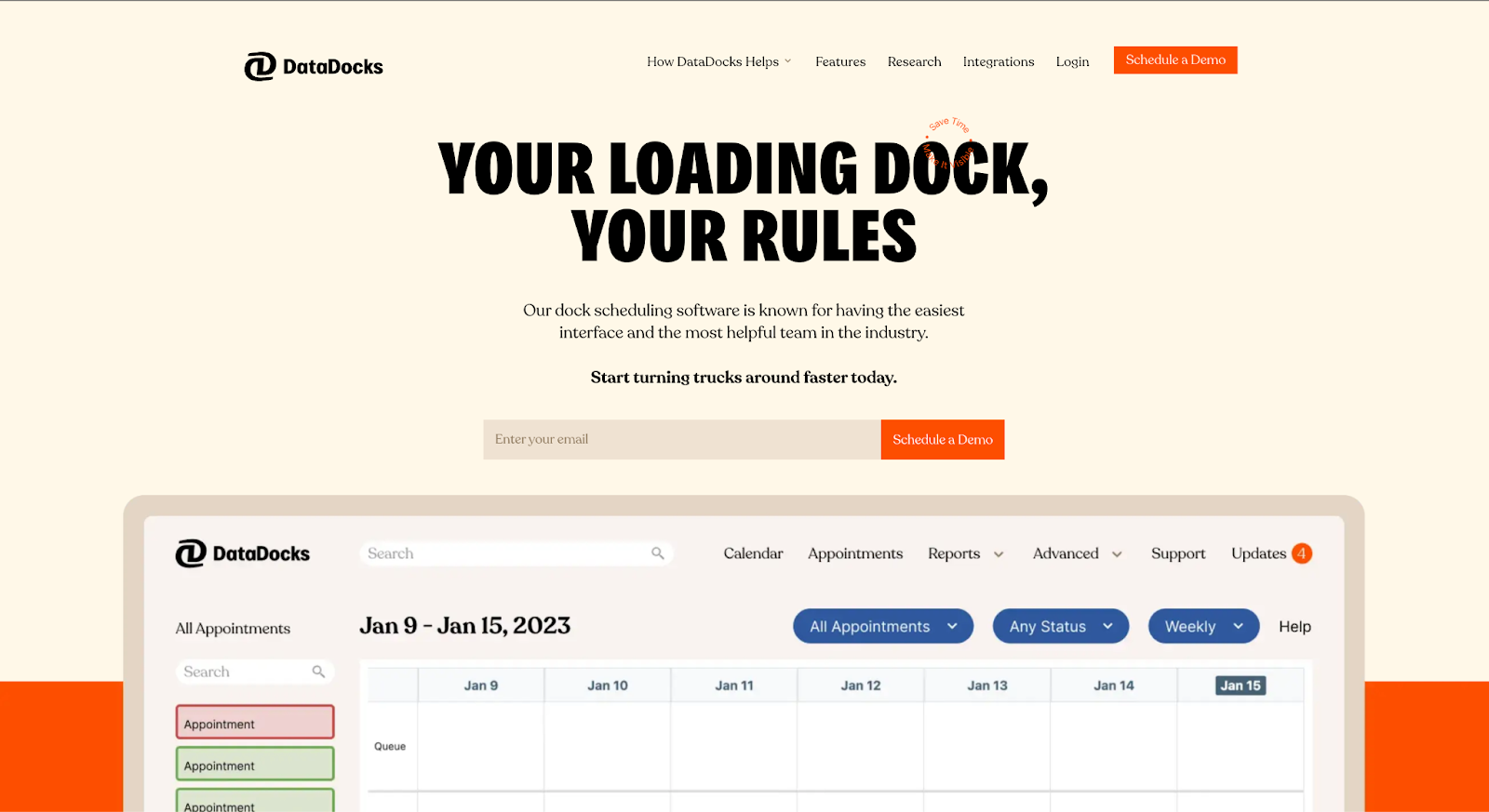
Launched in 2013, DataDocks focuses on one goal: make day-to-day yard and dock control effortless for high-throughput facilities. The platform is 100% cloud-native, so supervisors, planners, and carriers see the same live calendar, whether they’re at the guard shack, in the warehouse office, or off-site.
Strengths:
- Self-serve carrier portal. Carriers book, reschedule, or cancel slots online, cutting gate phone calls to near-zero.
- Real-time yard map. Drag-and-drop trailer moves update instantly for every logged-in user; colour timers flag aging loads before they clog doors.
- Rule-based automation. Allocate food-grade freight to sealed doors, block high-value loads after 22:00, or auto-approve trusted carriers—no coding needed.
- Live, multi-user editing. Schedulers, supervisors, and customer-service teams can work in the calendar at the same time without overwriting each other.
- Straightforward integrations. Pre-built connectors for leading WMS/TMS suites; flat-file and webhook options cover edge cases.
- Partnership-style support. Named success manager reviews KPIs each quarter and fast-tracks workflow tweaks into the roadmap.
Limitations:
- API depth is still growing. Current endpoints cover appointments and status updates; deeper analytics hooks are in active development.
- No stand-alone mobile app yet. The responsive web UI works well on phones, but an offline-first app is a little further down the roadmap.
Best for:
- High-throughput distribution centres and 3PL yards that handle a broad mix of freight and expect volumes and sites to keep climbing. DataDocks combines an intuitive live dock calendar, carrier self-service booking, and precise time-stamping, giving frontline teams immediate clarity and managers reliable performance data, without the heavyweight complexity of industry-specific systems.
Conduit
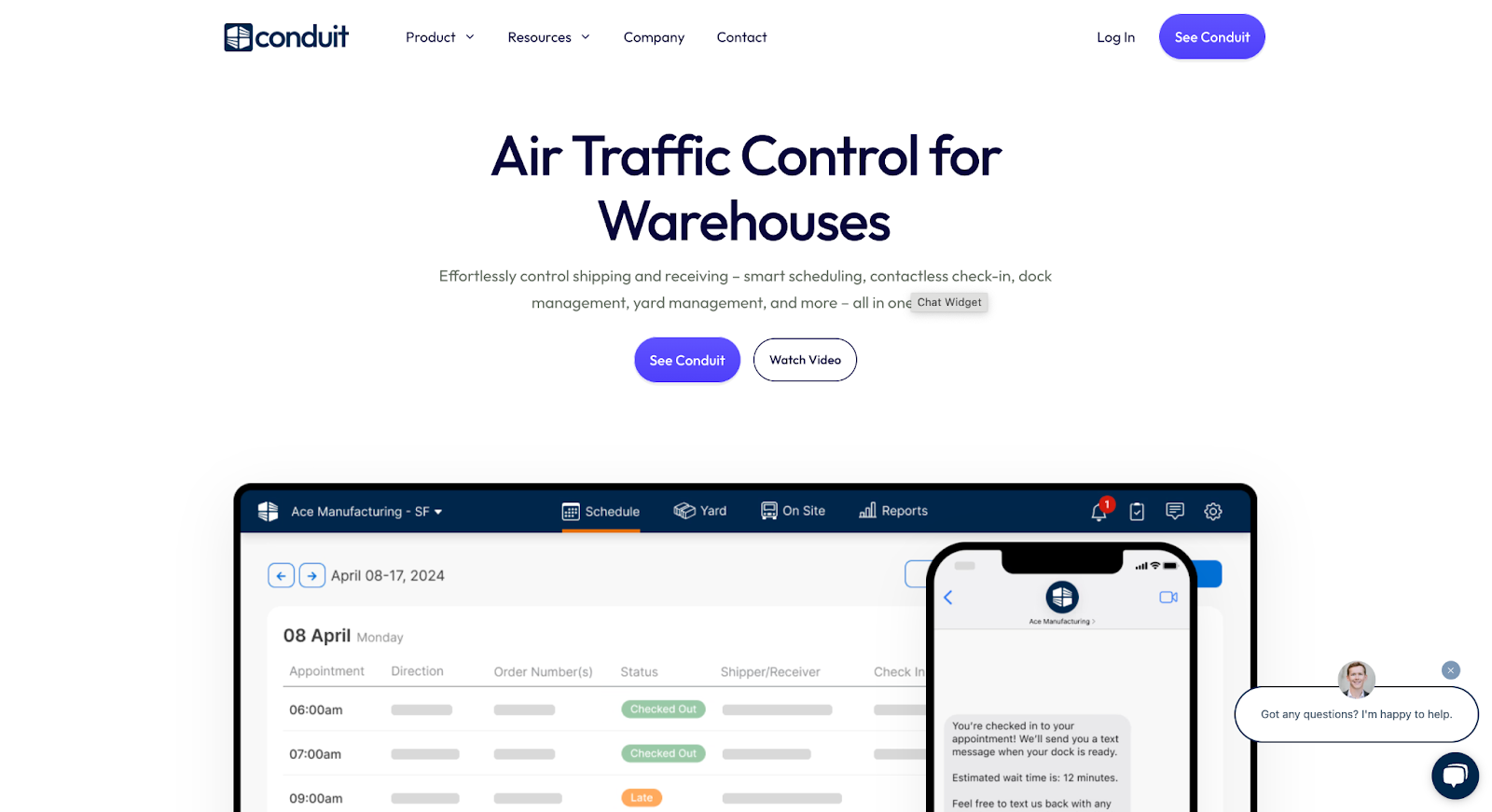
Launched in 2022, Conduit is the new kid on the dock: a slick, SOC 2-Type II-certified platform that bundles dock scheduling, driver check-in, and light yard tracking into a single, cloud-only app.
Think of it as the “iPhone-lite” of yard management: polished and deliberately prescriptive. You adopt Conduit’s workflows and get up and running quickly, without a heavy IT project or long configuration cycle.
Strengths:
- Driver-friendly check-in. QR codes and automated text messages shorten gate times and reduce radio traffic.
- Responsive product team. Early-stage culture means feature requests often turn into roadmap items within a release or two.
- Straightforward rollout. A single-site facility can move from contract to production in a matter of days, with minimal internal training.
Limitations:
- Static interface. Screen layouts and field sets are fixed; advanced users can’t tailor views or data capture to local processes.
- Documentation lag. Walk-through videos and help articles sometimes trail new releases, so recently added features can feel “undocumented.”
- Shallow yard orchestration. Conduit tracks trailer location but stops short of task sequencing, multi-site control rooms, or detailed dwell analytics… capabilities that become important once a yard handles dozens of concurrent moves.
- Entry cost (≈ US $7 k per site, per year). Reasonable for an established facility, but it leaves little room for pilot programs or seasonal pop-ups.
Best suited for:
Specialized freight forwarders, regional 3PLs, and bespoke manufacturers that run one or two yards with moderate throughput and place a premium on a clean driver experience. Operations that need network-wide visibility, granular task management, or highly configurable dashboards will reach Conduit’s ceiling quickly and typically graduate to a platform like DataDocks.
Opendock

Founded in 2018 and now part of the Loadsmart family, Opendock began as a pure dock-scheduling portal and, only recently, added a light yard-management add-on. Its strength is a pre-connected carrier network: many national fleets and freight brokers already use the platform, so slot adoption can happen quickly with little IT lift.
Strengths:
- Well-established integrations with Loadsmart, major carriers, and several freight-forwarder systems. Onboarding can be almost frictionless.
- Intuitive self-service scheduling for carriers: keeps phone calls to a minimum.
- Quick to deploy: most sites can publish an appointment calendar in a single afternoon.
Limitations:
- New YMS module is still limited: no task queueing, minimal trailer visibility, and few configuration options compared with mature providers.
- Workflow rigidity: users cannot change carrier details after creation and struggle to delete or cancel appointments cleanly.
- Reports of unprofessional customer support and surprise price jumps of 30-40% at renewal.
Best suited for:
Facilities with straightforward, live-load operations that work mostly with national carriers or large brokers and need a fast, low-touch scheduling tool more than deep yard control. Teams looking for dependable support, transparent pricing, and richer yard workflows typically move to vendors like DataDocks, where the feature set is comparable but the partnership experience is markedly stronger.
Samsara
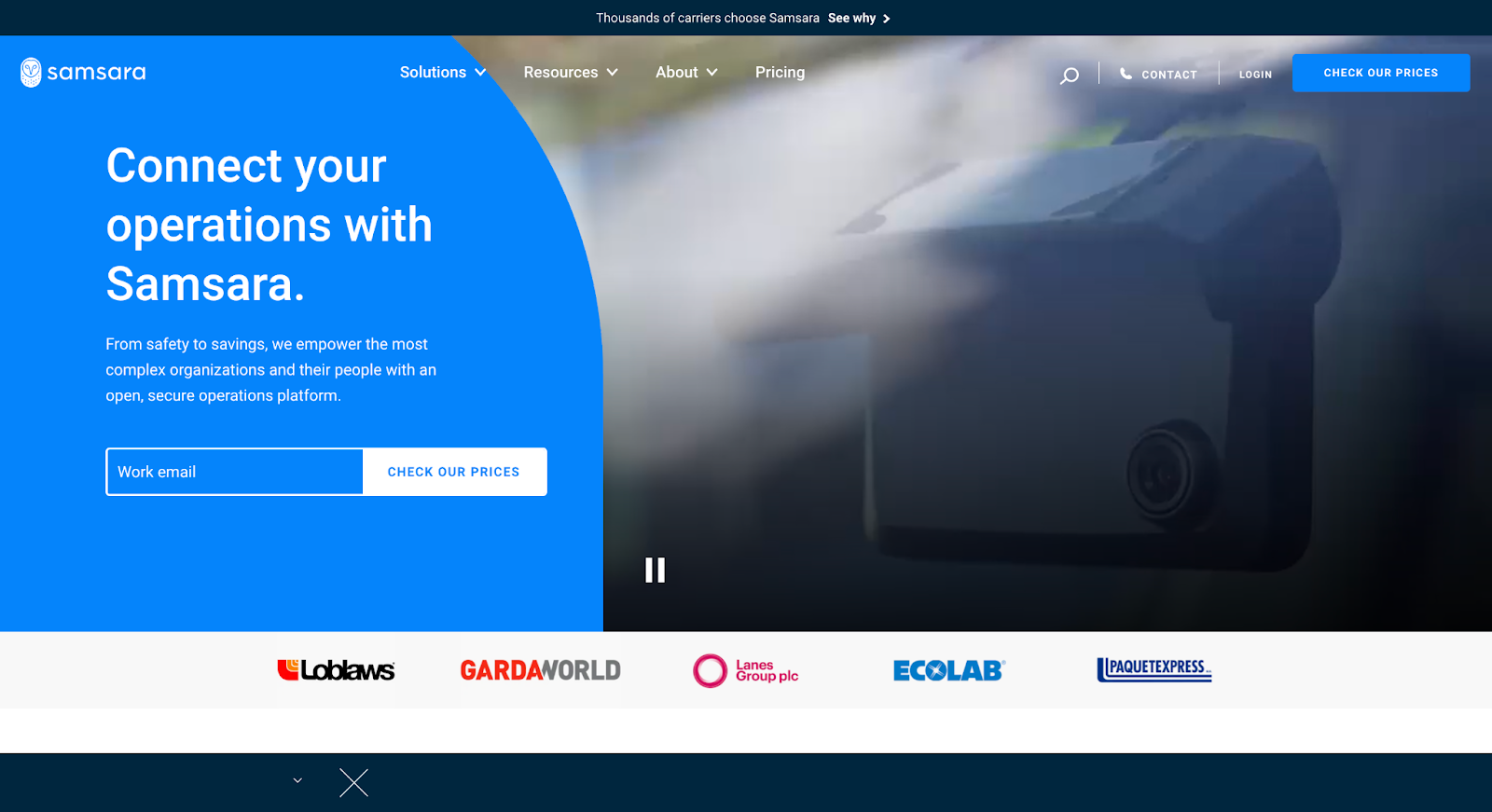
Founded in 2015, Samsara expanded from fleet telematics into what it calls a “Connected Operations Cloud,” layering a yard-management module on top of dash cams, ELD compliance, and sensor-rich asset tracking. The result is a single pane of glass for organisations whose own tractors and trailers dominate yard traffic.
Strengths:
- Fleet-first visibility. Second-by-second GPS and vehicle-sensor data feed precise ETAs, dwell times, and safety events into the yard screen.
- Built-in safety & compliance. AI dash cams, ELD, DVIR, and IFTA reporting live in the same portal, reducing vendor sprawl.
- Sustainability metrics. Idling, fuel burn, and emissions dashboards help corporate ESG teams benchmark progress toward electrification.
Limitations:
- Rigid commercial terms. Contracts typically run three years, and down-scaling or cancelling mid-term is difficult.
- Add-on pricing. Core yard workflows depend on extra-cost modules - trailer tracking, maintenance, computer-vision analytics - pushing up total spend.
- Steep learning curve. Yard users log into a fleet-oriented interface; non-drivers often need extra training to navigate menus meant for dispatchers.
- Support prioritisation. Mid-size warehouses report slower response times, especially when issues do not involve the fleet-safety stack.
Best suited for:
Shippers that run large private fleets, with perhaps 5 to 15% of moves handled by outside carriers, and who want yard data to sit alongside vehicle maintenance, safety, and compliance in one enterprise platform. Facilities where carrier variety is higher, or where custom workflows are the priority, tend to choose a partner like DataDocks instead.
Goramp

Founded in 2017 and headquartered in Vilnius, GoRamp focuses on quick-start dock scheduling and light yard visibility for European shippers. Its standout strength is language coverage and built-in compliance flags that make cross-border operations less of a headache.
Strengths:
- Simple, cloud-only set-up. Most sites are live in hours, not weeks.
- Wide language catalogue and EU-specific workflows (customs paperwork, driver ID rules) fit multi-country networks.
- Budget-friendly licensing keeps costs predictable for single-site operations.
Limitations:
- Limited configuration: no custom status labels, slot rules, or blackout-date planning for site closures.
- Mobile experience is basic, so guard-staff and yard-crew tasks still rely on desktop screens.
- Drop-and-hook tools are minimal; the platform is better at managing live-load traffic than trailer pools.
Best suited for:
Small to mid-sized warehouses that move freight across EU borders and need fast deployment, multi-language portals, and straightforward appointment control. High-throughput yards that juggle large trailer pools, or teams that want deeper task automation and richer mobile workflows, tend to gravitate toward vendors such as DataDocks, where configurability and real-time orchestration run several layers deeper.
C3 Yard
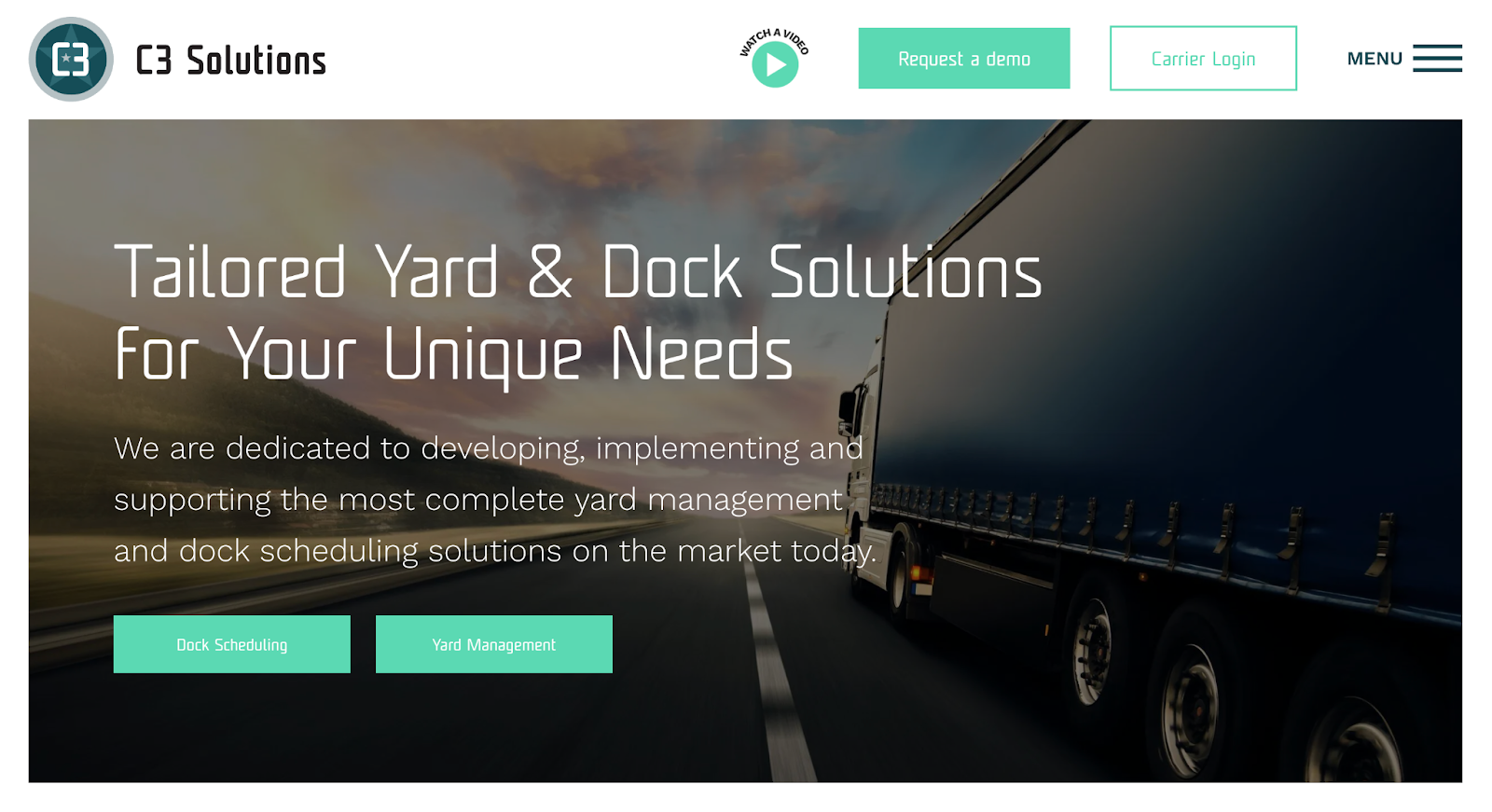
Founded in 2000 in Montréal, Canada, C3 Solutions has spent more than two decades building dock-scheduling and yard-management tools for highly specialized industrial sites. That heritage delivers plenty of depth, but the platform’s heavyweight design is often better suited to sprawling, compliance-heavy campuses than to the faster-moving yards most shippers run today.
Strengths:
- Handles edge-case workflows: internal shuttles between multiple plants, hazardous-goods zoning, temperature-controlled staging, without custom code.
- Around-the-clock support that can navigate complex regulatory or security requirements.
- Long track record with large manufacturers and 3PL campus operations.
Limitations:
- Noticeable slowdowns on busy days: the database architecture shows its age under high appointment volumes.
- Steep learning curve and heavy reliance on C3 consultants to build reports or tweak automation rules.
- Rigid roles-and-permissions model and older integration methods limit self-service API work.
- Premium pricing, yet everyday conveniences like automatic dock assignment, quick UI re-layouts, still require work-arounds.
Best suited for:
Multi-building manufacturing campuses or enterprise 3PLs that genuinely need granular safety logic and can absorb higher cost and complexity. Facilities that prioritise day-to-day speed, modern integrations, and flexible user management typically opt for vendors such as DataDocks, where reliability and ease of use come first.
YardView
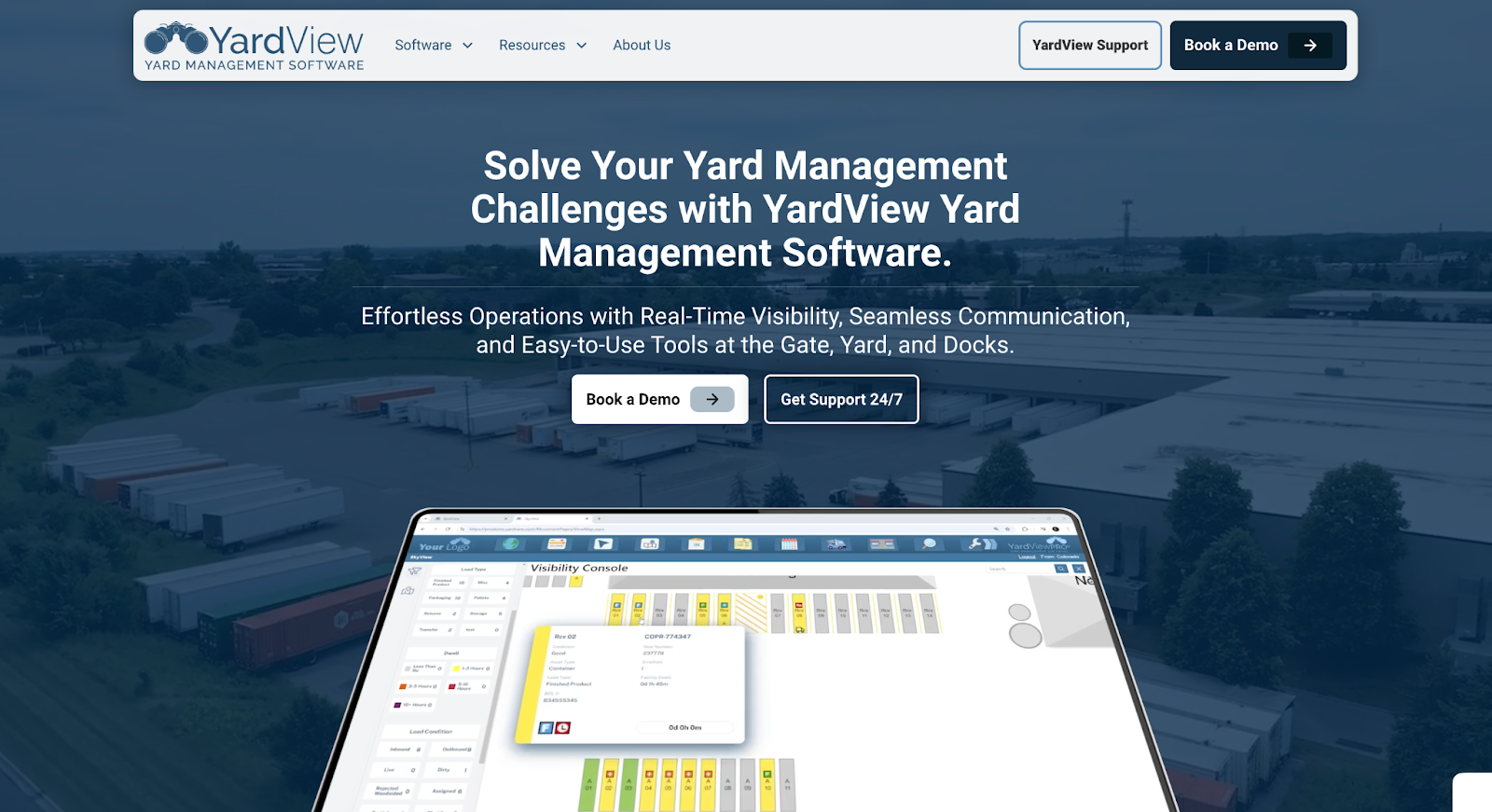
Founded in 1998 in Castle Rock, Colorado, YardView is one of the earliest dedicated yard-management providers. Its longevity means plenty of trailer-tracking depth, but the product still carries the DNA of a legacy Windows application, with a web layer added later for basic tasks.
Strengths
- Customer support team is consistently praised for rapid, hands-on help.
- Solid trailer-tracking toolkit: drag-and-drop moves, dwell-time alerts, inventory dashboards, at a mid-market price.
- Quick rollout for sites moving from clipboards or spreadsheets; most go live in days.
Limitations
- Full feature set depends on a Windows client; the browser version covers only the basics.
- Updates require every user to log out and rely on stable on-prem connectivity, outages can freeze the app.
- Interface is functional but dated, and power users find navigation slower than in newer SaaS tools.
Best suited for
Yards that handle mostly drop-trailers and want an affordable first step away from pen-and-paper workflows: regional distributors, food producers, and similar sites with straightforward dock operations. Teams that need mobile access, seamless cloud updates, or a modern UI typically choose platforms like DataDocks, which provide comparable trailer control without the legacy overhead.
Kaleris
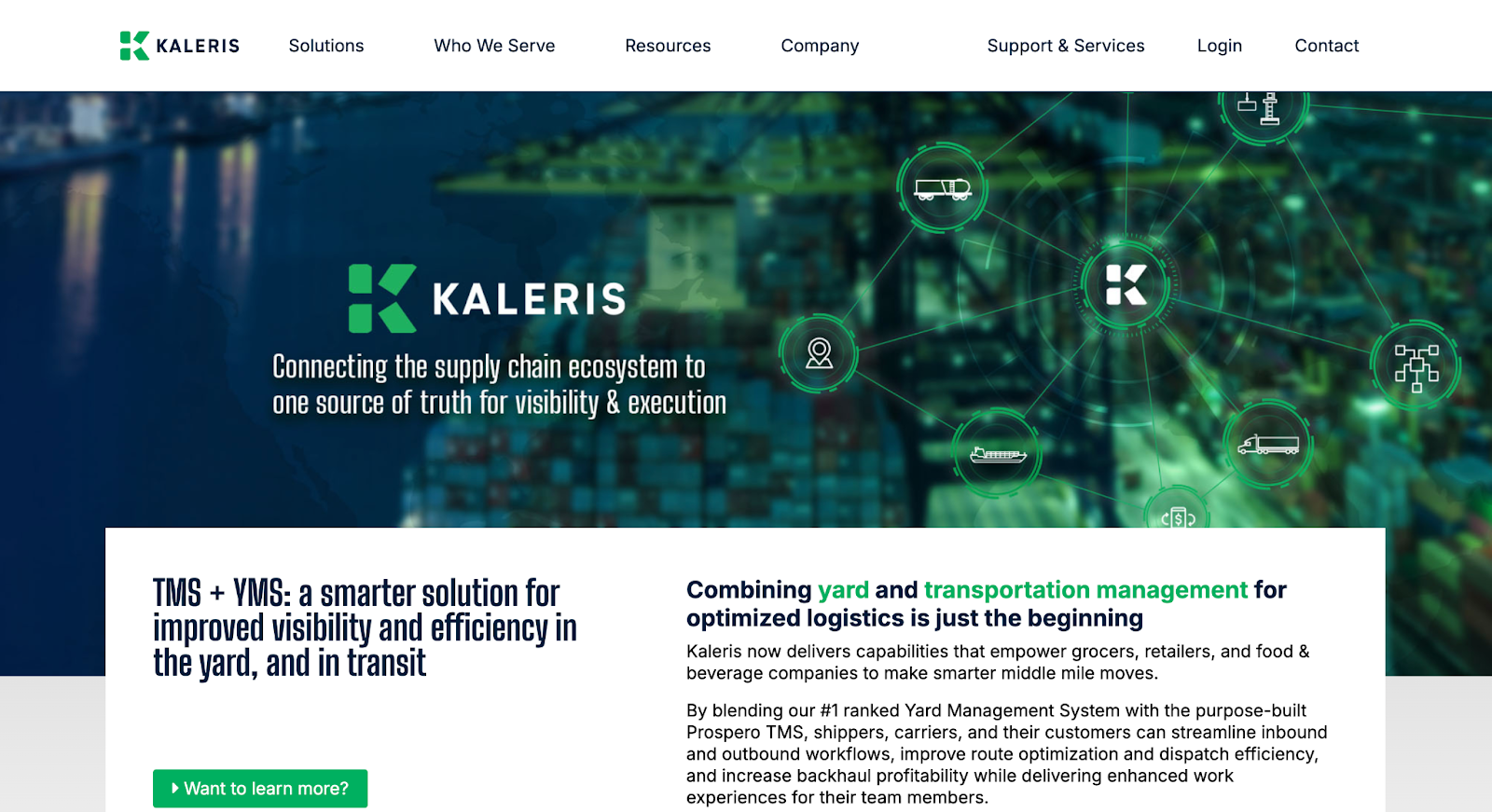
Born from the merger of PINC YMS and several terminal-software brands, Kaleris positions itself as a “Digital Yard” platform for asset-intensive supply chains: think ports, chemicals, and heavy manufacturing where RFID tags, GPS beacons, and reefer sensors are already standard kit.
Strengths:
- Deep RTLS footprint. Combines RFID, GPS, and IoT sensors for live pin-point tracking of trailers, railcars, and reefers.
- Marine-terminal pedigree. Native hooks into terminal-operating systems make it a natural fit for yards that sit behind a port gate.
- Broad feature catalog. Gate automation, shuttle dispatch, reefer fuel monitoring, plus more than 100 canned reports.
Limitations:
- Heavy configuration load. Site maps, sensor networks, and workflow rules all require specialist setup and periodic tuning.
- Slow enhancement cycle. Non-critical change requests can sit in queue for months, according to long-time users.
- Steep learning curve. The UI inherits elements from multiple legacy products, so training hours add up fast.
Best suited for:
Operations with complex asset mixes. Ports, energy terminals, large chemical or mining sites, where RTLS accuracy outweighs day-to-day agility. General-cargo warehouses that want quicker deployment and more responsive product evolution often favour DataDocks, which delivers core yard visibility without the overhead of a sensor-heavy stack.
4 Crucial Things to Look For in Yard-Management Software
1. Immediate Operational Impact
A yard system should start saving gate minutes and dock labour the very week it is switched on.
- 60-second supervised check-in. Guard staff or receiving clerks should be able to scan a BOL, print a pass, and direct the driver without the truck ever idling twice.
- Role-based control panel. Yard marshals see moves, dock planners see door status, finance sees dwell cost. No one needs a manual to find “their” screen.
- Visual urgency cues. Timers that turn amber at 45 minutes and red at 60 keep bottlenecks obvious without printing reports.
- Library of ready-made workflows. Need “cross-dock the mixed-pallet loads, live-load export freight, and quarantine damage claims”? Choose a template and tweak, don’t build from scratch.
If new hires can’t operate the basics by the end of their first shift, the tool is too complicated.
2. Elastic Capacity & Predictable Economics
Volumes jump before peak season; the software must absorb the shock without a rewrite… or a surprise invoice.
- Cloud horsepower that stretches. Screen refresh times should stay sub-two seconds when appointments double, not crawl to a halt.
- Real-world concurrency. Ask for proof the system still hums with 25–30 simultaneous users or 1 000 planned moves in a single day - the upper limit for most high-volume DCs.
- Bulk actions. Upload tomorrow’s 300 pallets or reschedule 40 appointments in one go, instead of click-by-click.
- Transparent price bands. Make sure adding a second yard or an extra hundred trailers doesn’t trigger a hidden “enterprise” uplift.
3. Partner-Level Support & Continuous Guidance
A yard never sleeps; neither should your vendor relationship.
- 24 x 7 live help that actually answers. Ask current customers how long a critical issue really takes to reach resolution.
- Quarterly health checks. The best suppliers review your dwell KPIs, spot creeping delays, and recommend tweaks before peak season.
- Road-map access. Operators’ suggestions should feed into upcoming releases. Otherwise technical debt piles up.
- Proven references. Speak with two facilities of similar scale; if both highlight prompt, practical support, you’re in safe hands.
4. Seamless Connectivity to the Rest of the Operation
A yard application earns its keep when its data flows cleanly into every other system that plans, pays, or reports on freight.
- Out-of-the-box links to WMS, TMS, and ERP. A door assignment in the yard should update inventory, labour, and ASN status automatically.
- Hardware readiness. The platform ought to accept scans from handhelds, pings from telematics, or reads from RFID gates with minimal middleware.
- Low-tech fall-backs. Clean CSV imports/exports and email notices are still vital when a partner’s system is down or a site is bandwidth-constrained.
Choose a YMS that masters these four fundamentals and it will keep delivering value, whether you’re turning 40 trailers a day at one cross-dock now or orchestrating a multi-site network in two years’ time.
Finding the Right Yard Management System For Your Needs Is Critical
The yard is the last “black box” in many supply chains; minutes lost at the gate ripple through labour plans, carrier scorecards, and inventory turns. Selecting the right YMS is therefore not just a software decision. It is a capacity, cost, and customer-service decision rolled into one.
In practice, the winners share four traits:
- Immediate operational impact – measurable gate-to-dock time savings within the first week.
- Elastic capacity and predictable economics – no slow-downs (or surprise price hikes) when volumes spike.
- Partner-level support and continuous guidance – real people who spot creeping dwell times before you do.
- Seamless connectivity – yard events flow straight into your WMS, TMS, ERP, and BI stack with minimal effort.
Where DataDocks Fits In
DataDocks was built around those four pillars from day one. Our interface is designed for supervisors, not software engineers. So new hires move trailers confidently by the end of their first shift. A cloud-native back end scales automatically during peak season, and our pricing stays transparent whether you operate one yard or a regional network.
Most important, customers don’t just “open a ticket”; they work with a named success manager who reviews KPIs, suggests workflow tweaks, and feeds frontline feedback into every quarterly release. And because our open API and pre-built connectors push real-time events into the rest of your stack, yard data finally pulls its weight in inventory, labour, and carrier-performance decisions.
See the Difference First-Hand
If you’re ready to turn your yard from a cost centre into a competitive advantage, let us show you what that looks like in a 30-minute walkthrough. No hype, no pressure. Book a demo with the DataDocks team and judge for yourself whether the four fundamentals are truly covered.