Warehouse management is a critical component of the supply chain, ensuring the efficient distribution of goods worldwide. The rapid growth of e-commerce, the increasing complexity of global trade, and the advancement of logistics technology are all contributing to the growing demand for skilled warehouse managers. This can be a lucrative career path.
If you already have one of these positions and you're thinking about how to move up to director, you can read our seperate guide on that topic.
This article will take an in-depth look at the job, its responsibilities, challenges and opportunities. Our aim is to give professionals, newcomers, and those considering a career shift an idea of what it takes to excel in this field. We will explore various facets of the role, including salary expectations, necessary qualifications, and recent developments.
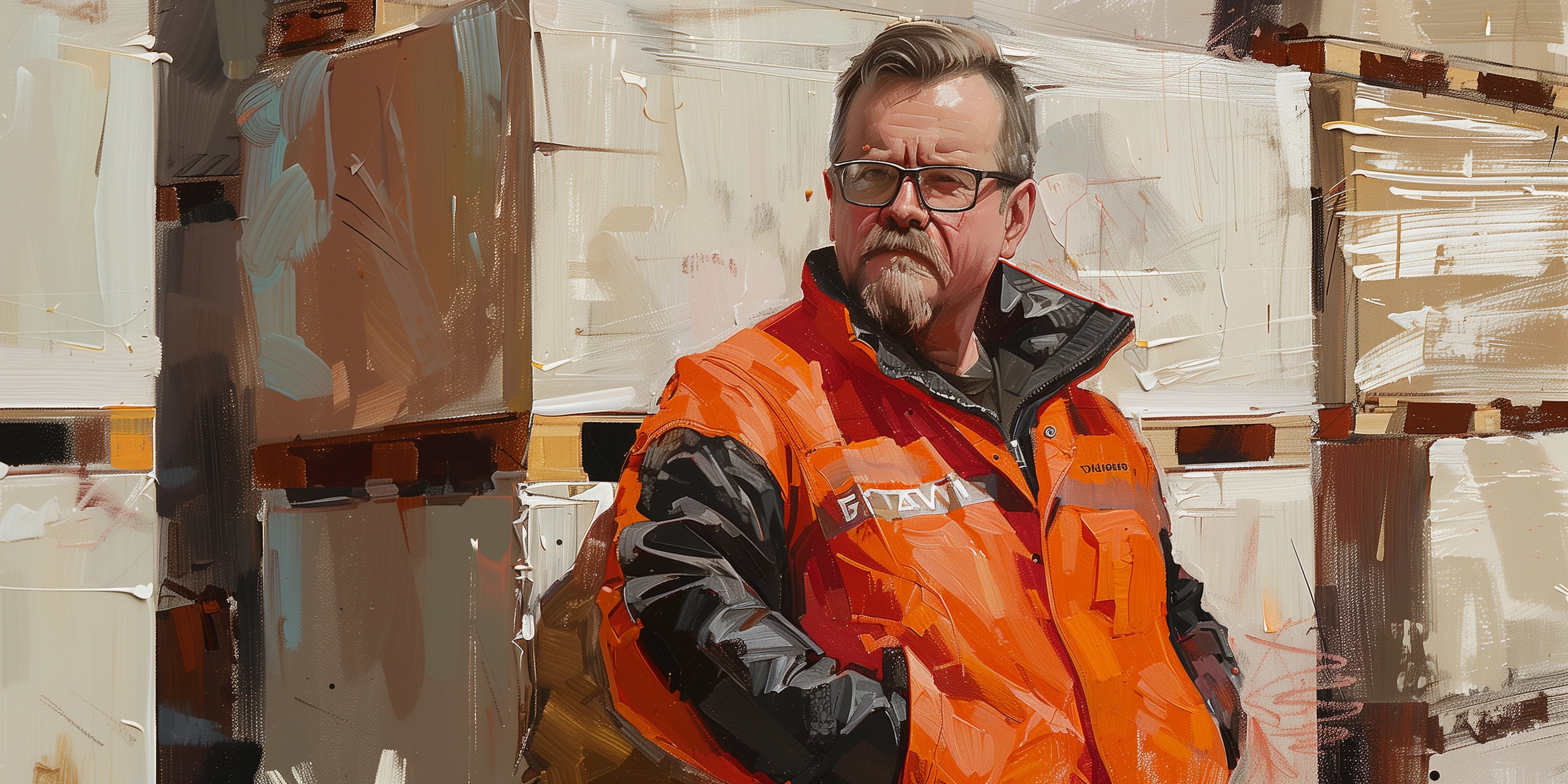
What Do Warehouse Managers Do?
Warehouse managers oversee all aspects of warehouse operations, ensuring that goods are received, stored, and dispatched efficiently and safely. They coordinate activities, from managing inventory levels to implementing new technology, all aimed at optimizing warehouse performance and ensuring compliance with safety and regulatory standards.
For a business, what happens in the warehouse directly impacts customer satisfaction and bottom line. Efficient operations ensure product availability and timely delivery, all while keeping costs under control. Furthermore, an effective warehouse contributes to better supply chain collaboration, which in turn enables more resilient and profitable business practices.
Workforce Development and Leadership
Warehouse managers are tasked with not only overseeing operations but also fostering a skilled, motivated, and cohesive team. This involves several key responsibilities:
- Recruitment and Training: They’re usually involved in the hiring process, selecting candidates who fit the operational needs and culture of the warehouse. Once hired, they ensure that new staff receive comprehensive training on warehouse procedures, safety protocols, and equipment operation.
- Performance and Safety Management: They monitor staff performance, providing feedback and coaching to improve efficiency, accuracy, and safety. This includes setting clear performance standards, conducting reviews, while also conducting regular safety drills, and addressing any hazards immediately to prevent accidents.
- Team Building and Motivation: They must cultivate a positive work environment through effective communication, recognition of achievements, and resolution of conflicts. Efforts focus on incentivizing performance, finding opportunities to acquire skills and knowledge, and coordinating team briefings to address challenges and updates.
Process Optimization
Warehouse managers constantly seek ways to refine processes and enhance productivity. That means critically evaluating and improving their processes and tools to reduce waste, while improving the ability of the warehouse to adapt to future needs or changes.
- Workflow and Resource Coordination: They orchestrate the receipt, storage, and dispatch of goods while optimizing workforce and resource allocation. This coordination ensures that all processes, from scheduling shipments to processing orders, are executed seamlessly and align with demand forecasts.
- Tools and Systems Implementation: They are often responsible for the selection, acquisition, implementation, and maintenance of both hardware and software. This encompasses a range of solutions from forklifts to warehouse management systems, ensuring that all tools are fit-for-purpose to enhance operational effectiveness.
- Budget Management and Profitability: They continuously look for opportunities to improve profitability, which sometimes means cutting costs, and sometimes means increasing short-term spending to unlock long-term efficiency, resilience, or innovation that creates business value.
Space and Inventory Control
Effective inventory control and management are fundamental to the success of warehouse operations. This area involves several activities for managers:
- Inventory Accuracy and Loss Control: They ensure stock levels are precisely recorded, while implementing systematic processes like cycle counting and spot checking. These also help in identifying and mitigating potential losses due to theft, damage, or administrative errors.
- Demand Forecasting and Inventory Optimization: They make judgments about what level of stock should be kept, aligning it with anticipated demands. This may involve analyzing past trends or communicating with sales teams. By avoiding overstocking or understocking, resources are used more efficiently and orders can be fulfilled on time.
- Efficient Space Utilization and Layout Planning: They aim to maximize warehouse space and optimize the layout for efficient material flow. This includes thoughtful placement of goods and strategic design of the warehouse floor to facilitate easy access and minimize movement, thereby increasing operational speed and safety.
Stakeholder Collaboration and Reporting
The work that warehouse managers do plays a pivotal role in overall supply chain performance. Their responsibilities extend beyond physical operations to encompass working with data and other parts of the business to ensure better decision-making:
- Safety and Regulatory Compliance: They ensure adherence to legal obligations, while implementing rigorous safety protocols to prevent workplace injuries. Depending on the industry, this may include managing cold chain requirements, maintaining a transparent audit trail and ensuring proper material handling practices.
- Collaborative Supply Chain Relationships: They develop and maintain effective partnerships with suppliers, transportation providers, and internal teams to enhance operational flow and supply chain efficiency. This sometimes involves negotiating terms and shared goals, and holding others accountable.
- Reporting and Performance Monitoring: They establish and track key performance indicators to assess operational efficiency and compliance levels. This may involve analyzing data, reporting findings to business leaders, and using insights to drive continuous improvement and strategic decision-making.
How Much Do Warehouse Managers Make?
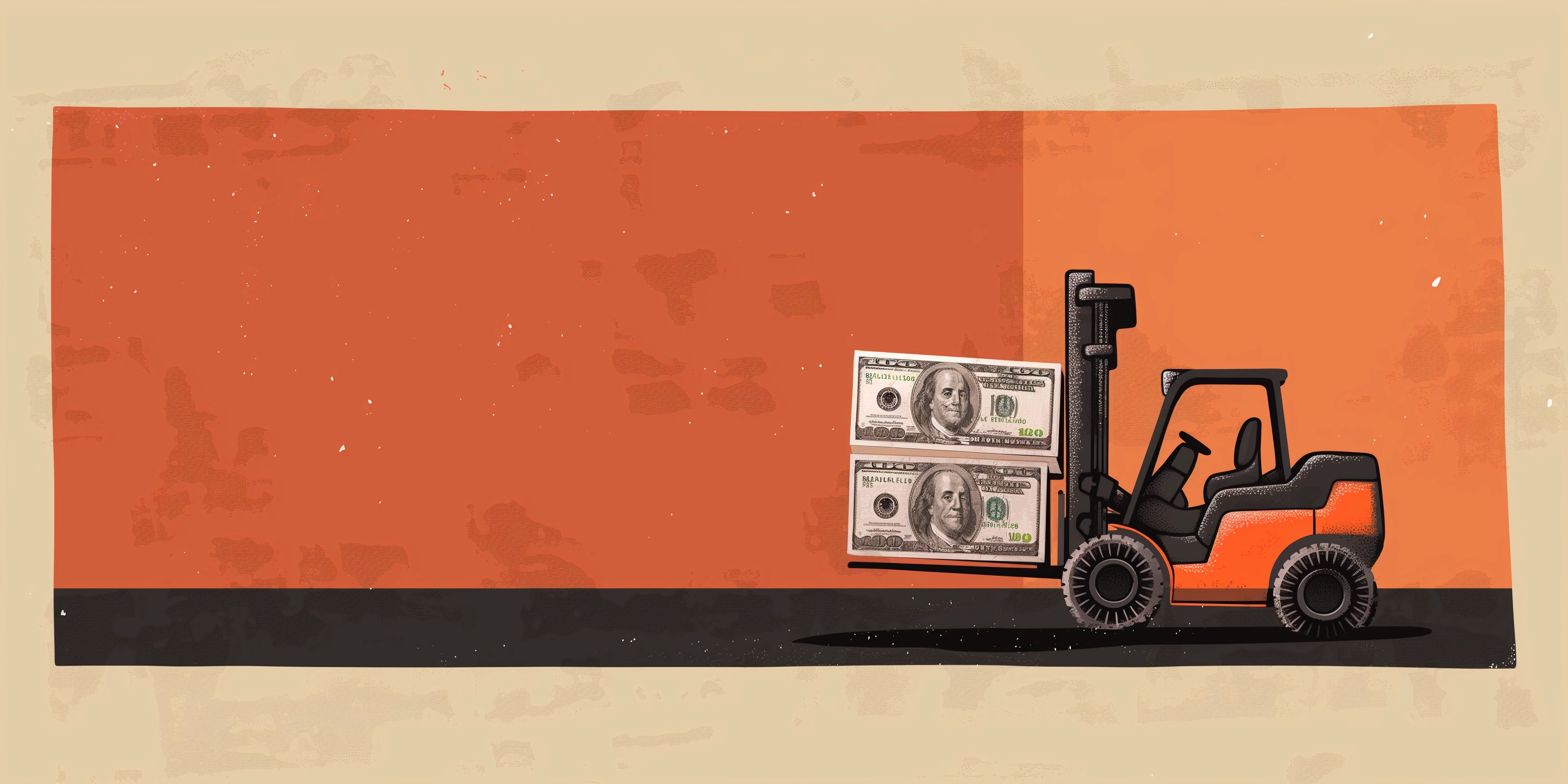
The median salary for a warehouse manager in the US is about $61,000 a year. That’s the average of estimates by indeed.com, talent.com, Glassdoor, Zippia, Comparably and Payscale.
But this figure can be misleading. Some warehouse managers are in charge of large, complex facilities in parts of the country where demand for their skills outpaces supply. These professionals might command upwards of $90,000.
At the other end of the scale, some warehouse manager jobs are mostly inventory management with some added responsibilities. Such positions are often open to candidates with no more than a high school diploma and a year or two of management experience, and might pay as little as $44,000 per year.
But which matters more: education, experience, location, or industry?
Factors Influencing Pay
Unlike many jobs, warehouse manager salaries don’t tend to increase the closer you get to an urban center. For the most part, warehouse managers’ pay differs from state to state in line with other salaries. But there are a few exceptions.
In states like Nevada, Kentucky, Indiana and Iowa, warehouse managers earn disproportionately more than their peers. In Utah, Minnesota and Alaska, it’s the reverse; warehouse managers are comparatively underpaid. The pattern generally reflects two things: the extent to which those states’ economies depend on logistics, and the amount of local competition for those jobs.
Earnings tend to be higher in the life sciences and pharmaceutical industries, in line with the additional complexity warehouse managers have to deal with. Besides that, salaries vary more between companies in the same industry than between industries per se.
Experience and education are the keys that unlock better-paying positions. Over the course of 10 years, a professional might expect to see their salary increase from $49,000 to $68,000. Warehouse managers with high school diplomas earn an average of $55,000; those with associates’ degrees $58,000; with bachelors’ degrees $71,000; and masters, $92,000.
But these averages don’t take into account the fact that highly-experienced warehouse managers tend to have more qualifications and vice-versa. In reality, one without the other is unlikely to be enough to get to the higher echelons, whereas having both gives you a good chance of landing one of those $90k+ positions.
How to Become a Warehouse Manager
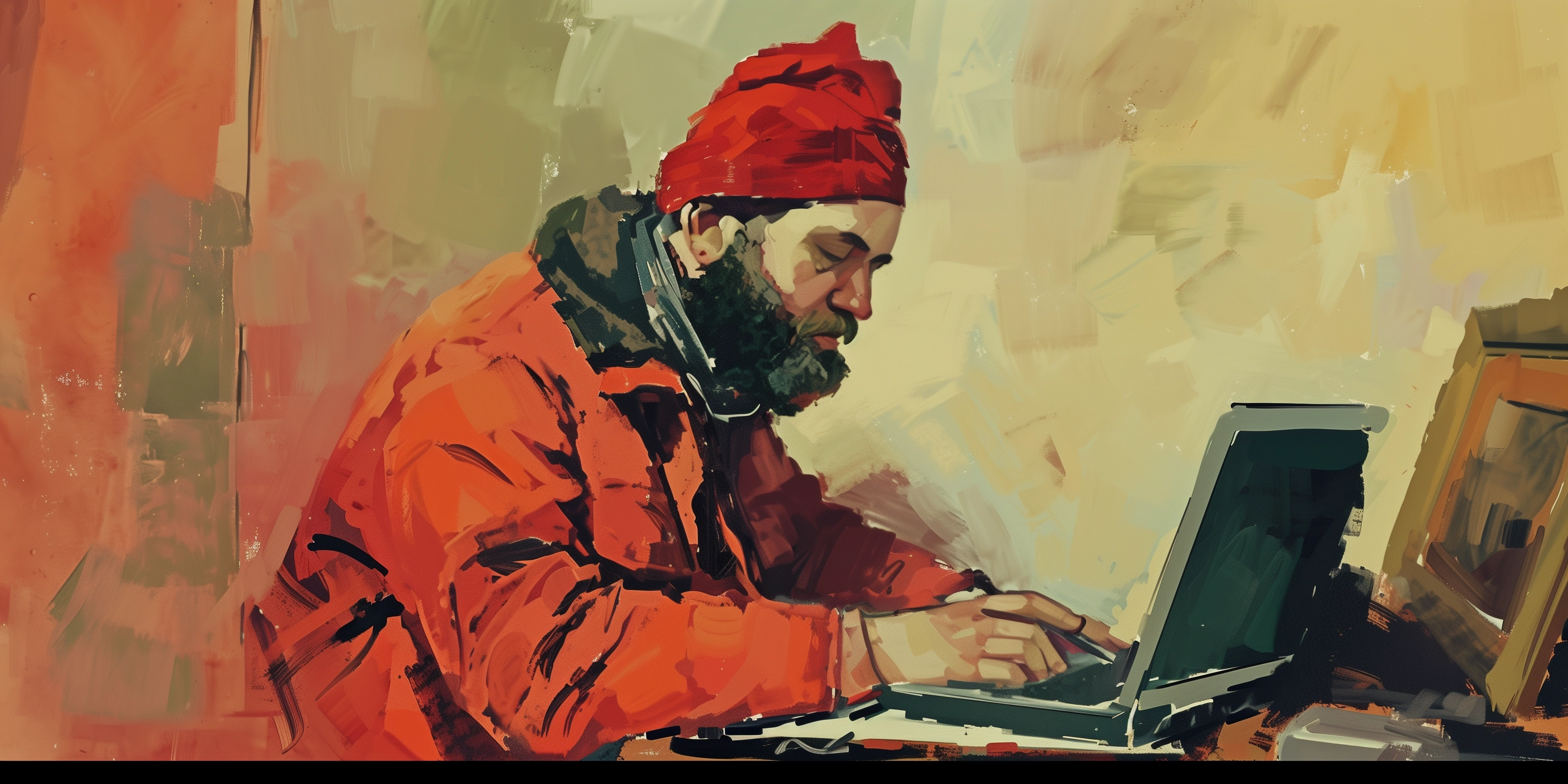
There’s more than one route into a warehouse management career:
- Advancing through the warehouse. Although this pathway requires a lot of initiative and often patience, some of the best warehouse managers started at the ground level, working their way up to supervisor and beyond, benefiting from mentorship along the way.
- Management experience outside the warehouse. It’s not uncommon for retail or production managers to transition into warehouse management. If you have a demonstrable record of leading people and optimizing processes, you already have a lot of the skills that matter in the warehouse.
- Lateral move from other supply chain roles. Procurement specialists, logistics coordinators, or supply chain analysts bring comprehensive supply chain insights. Their data analysis and supplier relationship skills offer a solid groundwork for effective warehouse management.
- Straight out of college. New graduates with degrees in supply chain management, logistics, business administration, or related fields enter the industry with current theoretical knowledge and modern management techniques.
That’s not to say that any of these backgrounds makes a candidate suitable for every warehouse management role. The needs of warehouses differ widely, and so does the management culture of different companies.
Building Your Warehouse Management Résumé
Securing your first warehouse management role requires the right mix of education, hands-on experience, and leadership skills.
There is no specific component that is essential to have on your résumé, but what you lack in one area you may be expected to make up for in others. It’s also worth considering that while some companies prize theoretical knowledge more highly, others prefer a seasoned worker with a proven track record of getting their hands dirty.
In terms of formal qualifications, candidates certainly benefit from having a bachelor’s degree in logistics, supply chain management, or business administration. But few companies demand that; rather, a certificate you can study for at your own pace will often suffice. The most well-known is the Lean Six Sigma Certification in Warehousing, but many institutions such as ASCM offer alternatives.
As for experience, the more direct exposure you’ve had to the warehouse environment, the better. This could take the form of material handling jobs or working as an inventory or shipping clerk. Most of all, at least a year or two directly supervising others, regardless of the industry or environment, demonstrates leadership and organizational skills that can be transferred to a warehouse management role.
Soft skills and other desirable qualities can be showcased in a few ways. Effective communication throughout the application process is one. Having a few anecdotes about how you’ve overcome challenges and developed people in the past is another.
Applying For Jobs and Acing the Interview
Securing a warehouse management position that aligns optimally with your skills, aspirations, and professional goals requires a methodical approach. Here are the steps to navigate your job search and interview process effectively:
- Strategic Job Selection: Rather than applying for every warehouse management position, look for opportunities that match your skills and ambitions. Read ads carefully for hints as to the size and complexity of the warehouse and what type of candidate they’re looking for.
- Tailor Your Applications: Customize your resume and cover letter for each application, highlighting your relevant experience and achievements. Focus on measurable outcomes and leadership experiences that directly relate to what they mention in the job ad.
- Research the Company: Before the interview, look into the company's market position and competitors. Having some knowledge going in means you can ask intelligent questions about their operations, demonstrating engagement that sets you apart from other candidates.
- Prepare Concrete Examples: Arm yourself with specific examples that showcase your operational awareness, problem-solving, and leadership skills. Be ready to discuss situations where you improved processes, led a team successfully, or implemented a solution that enhanced performance or reduced costs.
- Professional Dialogue: Initiate a discussion about the industry and current logistics trends. Use this as an opportunity to demonstrate your understanding of the broader business impacts of warehouse operations, including customer satisfaction, supply chain resilience, and financial health.
- Be the Interviewer: Prepare questions that reflect your engagement and assess company alignment with your career goals and leadership approach. Inquire about current warehouse challenges, the technologies they use, the company's future growth plans, and expectations for a warehouse manager in the initial 90 days.
- Follow Up and Evaluate Offers: Send a succinct follow-up thanking the interviewers for their time and reaffirming your interest. When reviewing offers, compare not just salary, but also the role's responsibilities, growth potential, and how well the company's culture and future direction match your career aspirations.
How to Be an Effective Warehouse Manager
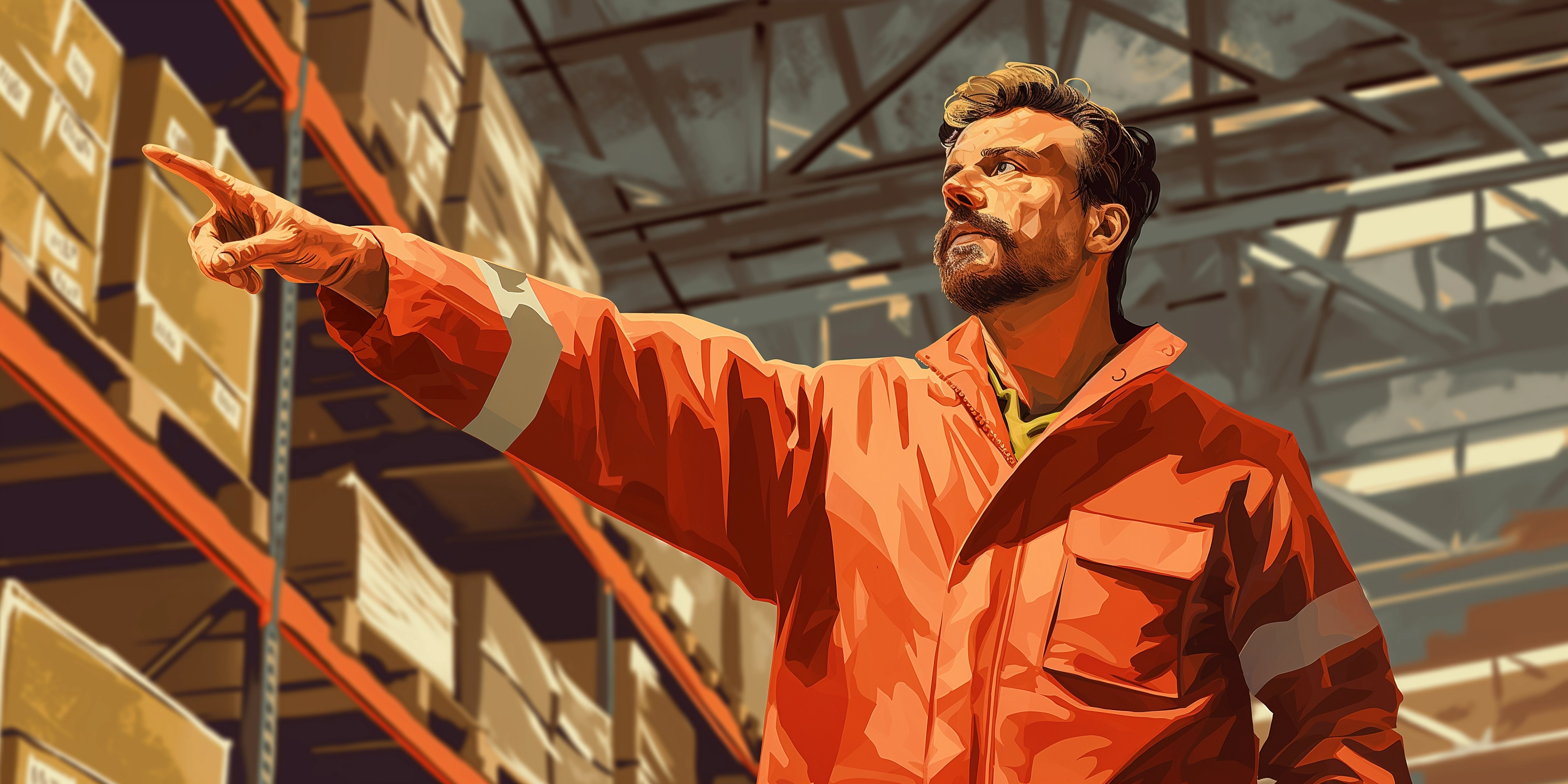
Good warehouse managers have their methods that work, but great warehouse managers know how to read the specific operational situation and adapt to the environment.
Warehouse management is a series of balancing acts: between the tried-and-true and experimenting to unlock better performance, between change and consistency, and between simplicity and rigor.
Every strategy has its advantages and disadvantages. And when it comes to adopting new technologies, there’s no such thing as the perfect moment. The key lies in making informed, timely decisions that align with current needs and future goals, despite the ever-present uncertainties.
Warehouse Management Strategies
- Wave Picking v.s. Zone Picking: Wave picking optimizes resource use and scheduling, ideal for batch orders, but can cause downtime between waves. Zone picking enhances continuous activity and reduces cross-warehouse travel but demands sophisticated tracking and coordination.
- SOP-reliance v.s. KPI-reliance: Stricter enforcement of standard operating procedures reduces variability in processes, thus mitigating risk. On the other hand, putting KPIs at the heart of your management approach shifts the focus towards outcomes, encouraging innovation and fostering a dynamic, flexible environment.
- Role Rotation v.s. Specialization: Role rotation diversifies employee skills, enhancing adaptability and coverage, but may dilute specialized expertise. Specialization can increase performance in key areas but may limit operational flexibility. Either approach may be better for morale, depending on the team.
- Just-in-time v.s. Just-in-case: JIT has been the favored inventory management paradigm for most of the 21st century because it can achieve incredible cost savings. It demands precise scheduling and robust supplier relationships, and thrives in stable, predictable environments. Conversely, JIC, which is gaining favor in response to recent global disruptions, advocates for maintaining higher levels of safety stock, ensuring continuity in the face of unexpected challenges, albeit with increased holding costs.
- Seasonal-Intuitive Placement v.s. Continuous Analysis: Making use of your experience and past trends to pre-emptively organize inventory prior to seasonals shifts fosters operational stability. In contrast, ongoing reassessment and reorganization of inventory enhances the warehouse's ability to adapt quickly to external changes, but can be disruptive and labor-intensive.
- ABC, Bin sequence, or Random Sample Cycle Counting: In ABC cycle counting, items are categorized based on their value or turnover rate, with 'A' items counted most frequently due to their higher importance. Bin sequence counting is easy to organize, and aligns with the physical layout of the warehouse, ensuring every location is regularly checked. Random sample counting, on the other hand, offers unbiased data but can miss systematic errors.
- Kaizen Approach v.s. Business Process Re-engineering: Kaizen emphasizes continuous, incremental improvements focusing on eliminating waste, ideal for managers aiming to foster a culture of employee involvement. BPR can be better for those who have identified clear bottlenecks and have a strong operational vision, allowing for large-scale elimination of redundant processes, thus leading to major improvements in productivity and cost reduction.
- Separate inbound and outbound areas v.s. Flexible Docks: Opting for separate inbound and outbound areas can ensure a clear division between different stages of the warehouse workflow, minimizing handling errors. However, implementing flexible docks helps cater to fluctuations in shipment sizes and schedules, which can be particularly beneficial in environments with varying peak times. This adaptability can lead to improved resource allocation and throughput, but requires careful planning to prevent confusion and maintain efficiency.
- Trucks FIFO v.s. Carrier Punctuality Incentives: Having a first-in-first-out policy in the loading dock provides a predictable method for handling shipping and receiving. Transitioning to a system that prioritizes trucks based on their adherence to scheduled arrival times can significantly reduce idle times and encourage carrier cooperation, but it demands a more nuanced approach, balancing strict scheduling with the flexibility needed to accommodate unexpected delays and prioritize urgent shipments.
Implementing Technology and Innovation
Warehouse managers often feel like there’s no time to spare for big change projects. They’re too busy keeping everything running.
What’s more, there’s a real risk of such projects failing, either because a new technology doesn’t perform as expected, or the behavioral change needed to accompany it never manifests. It’s also not always clear whether certain technologies are ‘too young’ or actually on the point of being made obsolete by a superior alternative.
Case-in-point, RFID (Radio Frequency Identification) technology allows for real-time tracking of inventory without direct line of sight, significantly improving inventory accuracy and labor efficiency. It enables quick identification and localization of products, reducing picking errors and speeding up inventory audits.
Implementing RFID is a big project, requiring extensive collaboration with supply chain partners, the purchase of special equipment, and training warehouse staff on a whole new set of processes. The companies that successfully implemented it in the early 2010s reaped the benefits, and a chorus of consultants says: everyone should be doing this.
On the other hand, people also say that RFID will be out of date in a few years! IoT (internet-of-things) sensors are getting smaller, cheaper, and more reliable, while simple barcode scanning is better than ever. Alternatives like BLE (bluetooth low-energy) and NFC offer longer range, easier integration and more data bandwidth than RFID.
Yet for many operations, RFID still makes more sense because it’s the industry standard. Employees are more used to it, supply chain partners are more prepared to work with it, and even if its future isn’t bright in the long term, at least it’s predictable.
Another big technological trend is Predictive Analytics. The potential to transform warehouse operations through accurate demand forecasting and resource optimization is immense. Yet, the practical application often stumbles over the steep learning curve and infrastructure requirements. Many warehouses lack the data foundation and analytical skills necessary to harness its full power, leaving a gap between its promise and its practical utility.
Dock Scheduling is the one technology that is both mature and in no danger of becoming obsolete. In fact, its role will get bigger as supply chains get hungrier and hungrier for data at every point in operations. It hits the sweet spot of being relatively straightforward to implement, while also having a significant impact on efficiency, because it takes the most unpredictable process in the warehouse - shipping and receiving - and gives it some structure.
Implementing dock scheduling software can optimize loading dock operations by coordinating arrivals and departures. This technology helps reduce wait times, streamline the flow of goods, and improve carrier turnaround times. Not only does it streamline current operations, but also establishes a data-driven framework that sets the stage for integrating advanced technologies like RFID and predictive analytics.