In a distribution center, every cog in the wheel plays a vital role, but the impact of dock scheduling is often underestimated. It has the power to impact everything, from cost efficiency and throughput speed, inventory accuracy and customer satisfaction.
DCs face unique challenges, ranging from managing high volumes of materials and load variability to handling diverse SKU lineups and cross-docking operations. Mistiming, miscommunication, or even the smallest of errors can amplify these challenges, leading to costly disruptions.
This article explores the crucial role dock scheduling plays in seven key scenarios of complex DC operations and highlights how the right software can make a world of difference. The advantages offered by a system like DataDocks not only help manage these complexities but also enable a more strategic and efficient approach to your operations as a whole.
For a concise overview of the core dock-scheduling principles this article builds on, check out our Intro to Dock Scheduling 101.
Dealing with High Pace and Volume of Goods
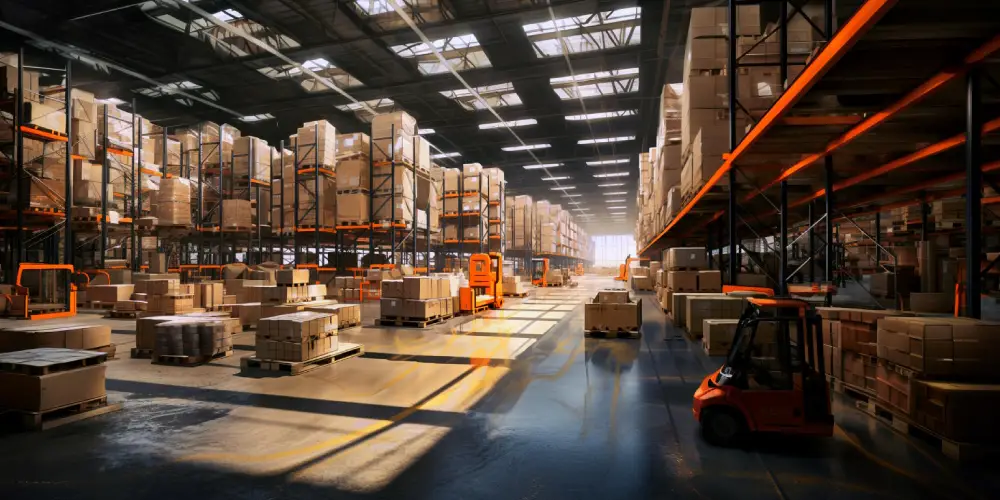
Coordination of shipments is challenging in high-volume operations. The potential for delays is significant, and each one can start a domino effect, leading to detention fees, excessive overtime, and congestion inside and outside the facility. This environment makes effective dock scheduling indispensable.
Fast-paced facilities need a two-pronged approach of proactive planning and rapid response to change.
Proactive planning starts with staggering shipment schedules throughout the day to prevent congestion. It also means aligning staffing schedules with peak operation times to reduce the strain on your workforce.
On the other hand you must be prepared for surprises. If your dock scheduling platform is not set up to handle change at scale, all your meticulous planning can fall apart during a demand spike.
Careful management of relationships with carriers is another critical aspect of dealing with high pace and volume. By fostering good communication, sharing scheduling expectations clearly, and being open to feedback, distribution centers can get the best out of their transportation partners and build in some resilience to disruption.
In more complex logistics situations, reporting and forecasting are key. Insights from data can reveal bottlenecks, and help spot potential spikes in demand in advance. This empowers distribution centers to anticipate, rather than react, and to fine-tune their activities for maximum efficiency.
Retail Dock Scheduling: Managing Load and SKU Variability
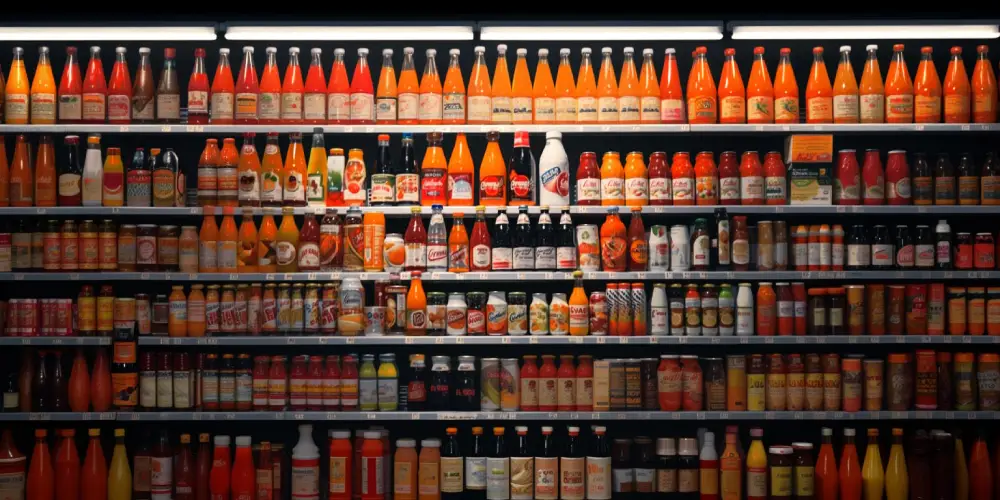
A diverse lineup of SKUs tends to go hand-in-hand with greater fluctuations in contents and size of loads. This variability presents a challenge - each load is unique. While one truck may carry a large amount of a single SKU, the next may contain a mixed load of many different items. These factors complicate inventory management and, in turn, affect the coordination of loading and unloading slots.
A sophisticated dock scheduling system like DataDocks can be configured with rules to deal with this complexity. For example, certain SKUs, carriers, or shipment volumes can be restricted to specific dock doors or times of day. With a tailored ruleset, the scheduling system can navigate the challenges of diverse SKUs and fluctuating volumes, ensuring each shipment is handled accurately and efficiently.
The risk of mis-shipments and stock discrepancies is another critical factor. When dealing with many SKUs and load types, errors can lead to significant inventory mismatches. Precise dock scheduling creates the conditions for more robust inspection and reporting, which mitigates this risk.
Storage space constraints, due to the high SKU count, bring yet more complexity. Strategic placement of goods within the distribution center, based on their loading and unloading schedules, becomes crucial. The information generated by your dock scheduling software can inform placement decisions, as it will become clear what factors contribute to longer loading and unloading times.
Scheduling Shipments for Cross-Docking Operations
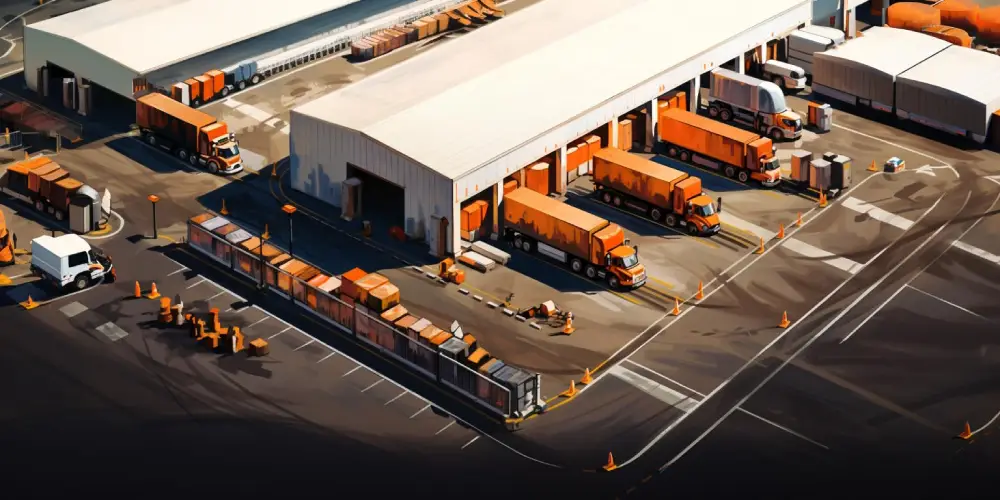
In a typical warehouse, products are often stored for some time before they are moved out. However, with a cross-docking strategy, the primary goal is the swift and seamless transfer of goods from inbound to outbound trucks, thus minimizing or eliminating the need for storage.
A load arriving earlier than scheduled doesn’t necessarily present a major problem for many environments. But with a cross-dock, early can be just as bad as late. If inbound loads are leaning early while outbound leans late, you end up with congestion on the floor.
DataDocks provides a robust solution to this challenge with its suite of powerful features tailored to support the demands of cross-docking. It allows managers to monitor the progress of shipments and adjust the schedule in real time as situations on the ground evolve. Automatic notifications for changes give operators peace of mind and ensure every participant is up-to-date on the schedule.
Efficient yard management is also paramount in a cross-docking scenario. DataDocks offers a live view of your yard, facilitating swift and informed decisions to streamline workflows. This visibility significantly reduces dwell times and prevents congestion.
Cross-docking operations introduce unique scheduling challenges due to the immediate transfer of products from inbound to outbound vehicles. However, with a comprehensive dock scheduling solution in place, these challenges can be adeptly managed to maximize operational efficiency.
How Dock Scheduling Helps with DtC and Multi-Channel Fulfillment
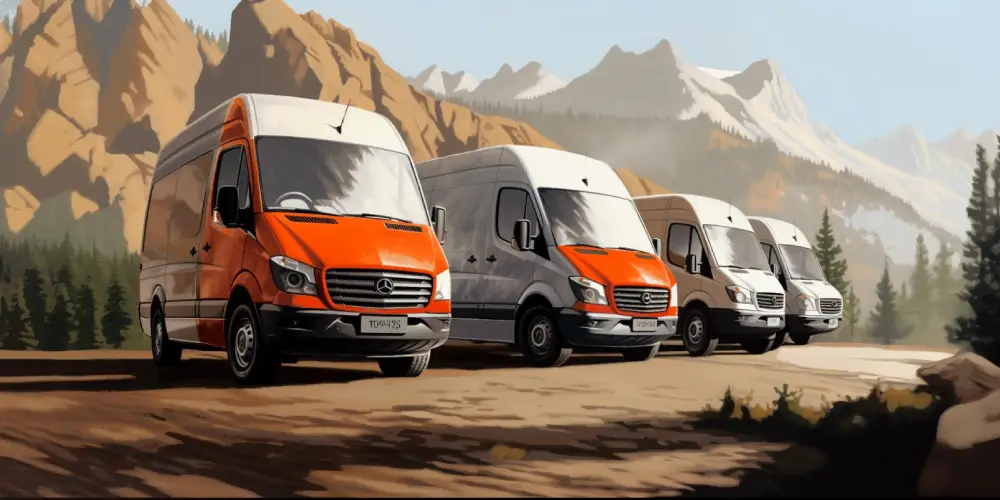
In direct-to-consumer businesses, the high volume and variability of loads typically result in complex shipping processes. This is especially true given the end customer’s demand for fast delivery.
However, the implications for receiving are just as significant. Managing inbound logistics effectively is paramount to ensuring downstream activities can run smoothly. Stockouts, overstocking and misplacement can be disastrous for DtC operations.
A robust dock scheduling system takes care of this. Real-time monitoring expedites order processing, while intelligently adjusting to fluctuating demand. By validating incoming data, the system safeguards accurate inventory counts, which helps with customer satisfaction. Plus, it highlights bottlenecks, tracks performance, and measures carrier punctuality, opening a clear path for continuous improvement.
What if your distribution center is responsible for not only DtC fulfillment, but wholesale or retail replenishment as well? Each channel has its unique requirements and schedules, which add another layer of complexity to dock scheduling.
Once again, a fit-for-purpose dock scheduling platform is instrumental in ensuring success. It’s not just internal processes that must be managed closely but coordination and communication with external partners. An easy-to-use and highly customizable carrier portal like the one provided by DataDocks makes that possible.
Appointment Booking for Numerous Carriers or Mixed Fleets
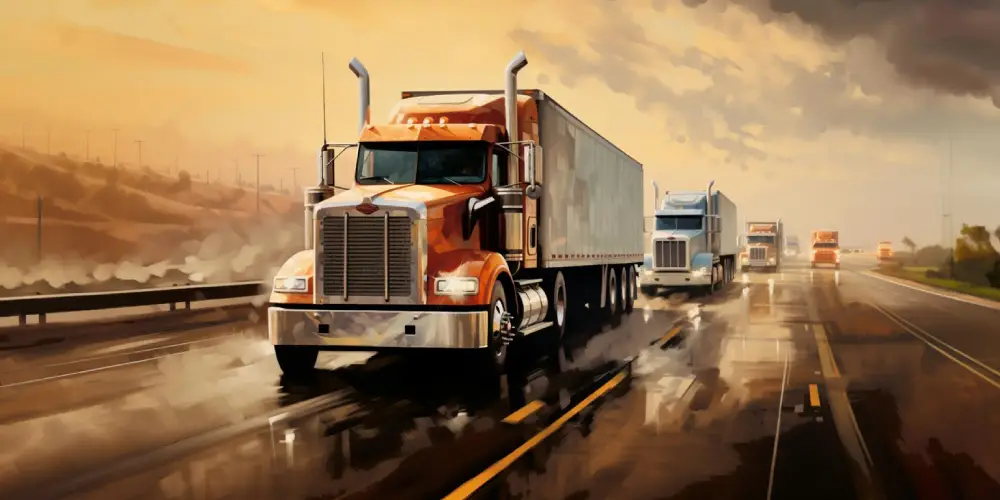
Managing multiple carriers or keeping track a mixed fleet of owned and third-party vehicles adds some complexity to logistics. Coordination at the loading dock is one facet of this challenge.
Getting carriers to self-book online is one of the best ways to reduce the pressure. That doesn’t mean you never pick up the phone again, just that the basic process of arranging time slots is automated.
Next, having live visibility of your yard can greatly contribute to maintaining an organized flow and reducing turnaround time. When every trailer, whether it belongs to your organization or a third-party, can be tracked in real time, it’s much easier to stay in control.
An organized yard also helps minimize detention charges. By keeping tabs on the dwell time of each trailer and ensuring trailers are promptly moved from the yard to the dock or onto the road, you can mitigate the risk of incurring these fees.
Equally important is the ability to forecast and manage your yard capacity effectively. When you can predict the volume of inbound and outbound loads accurately, you can prevent overbooking and the subsequent congestion in your yard. This proactive approach enables you to maintain a smooth process flow, even during peak times.
Moreover, strategic allocation of dock doors based on the nature and urgency of shipments can also significantly enhance your operational efficiency. This requires a thorough understanding of your loads and their priority levels, something that becomes easier with software that provides a comprehensive view of your yard and its activities.
The Role of Loading Dock Management in Reverse Logistics
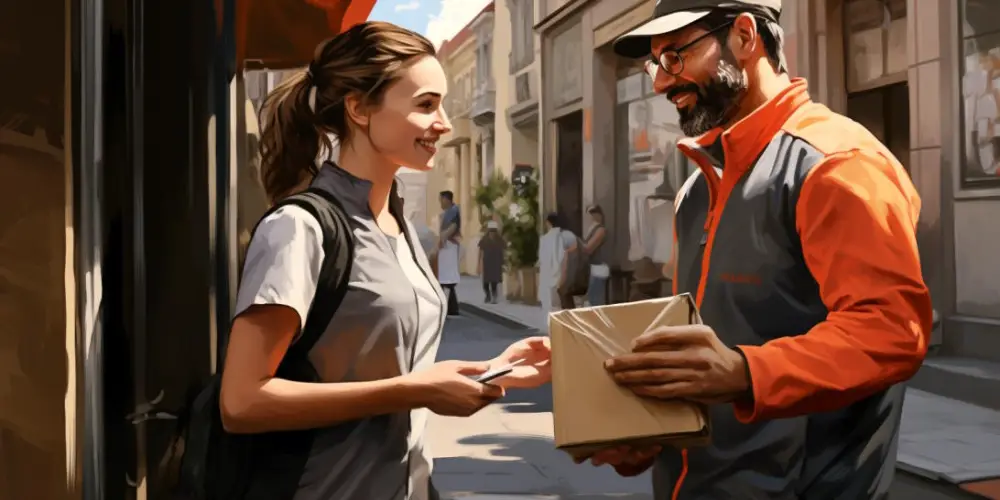
For those facilities handling returns, repairs, or recalls alongside conventional logistics, resource allocation can be a puzzle.
Products coming back into the facility often need additional processing. Certain goods might require inspection, refurbishment, disposal, or restocking. Others may need to be returned to the manufacturer. Each of these processes takes time and can lead to a backlog if there isn't a well-structured plan in place.
Internal stakeholders may need visibility on when certain shipments are expected and what they contain. By digitizing the way you manage appointments, you can make sure this kind of data is always available to those who need it.
DataDocks also allows you to set up a sophisticated algorithm of capacity limits, ensuring the receiving area doesn’t get overwhelmed. For instance, you might dedicate specific dock doors or time slots to reverse logistics and prevent mix ups between different channels.
Data is king when it comes to managing reverse logistics. The power to analyze what’s coming in, identify common reasons for returns, and spot patterns can help organizations anticipate and prepare for the commercial implications.
How Dock Scheduling Integrates with Automated Systems and Hardware
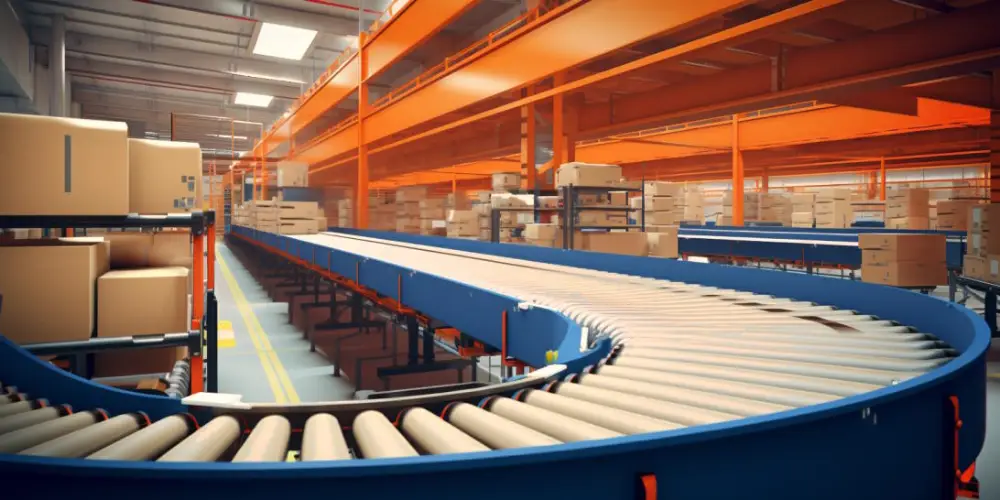
In recent years, there's been a considerable surge in the adoption of advanced hardware in distribution centers. Automated storage and retrieval systems (AS/RS), conveyor systems, robotics, and sortation systems minimize manual intervention and, when they work well, reduce errors. However, to maximize these benefits, controlling these systems with centralized software is key.
The problem is, software that can do everything tends to do nothing particularly well. For example, even the most sophisticated warehouse management software with great automation features tend to do a poor job at dock scheduling.
Fortunately, DataDocks can speak to those systems through an API. The closer you can get to end-to-end visibility where information is shared between every point of the supply chain, the better decisions you can make.
Automated systems can also generate a wealth of useful data. For instance, certain SKUs might require more processing time. These trends can then help inform even better dock scheduling rules, like allocating extra time for loads that are expected to be difficult.
In a highly automated environment, swift reaction to disruptions is essential. If an unexpected delay occurs at the loading dock, it could have a ripple effect on the subsequent automated processes, and vice-versa. Live notifications about such changes enable quick adjustments to the workflow.
Why DataDocks is the Ideal Solution for Distribution Centers
Operating a distribution center successfully is a complex endeavor that demands meticulous attention to details and strategic foresight. Dock scheduling may seem like a small piece in the puzzle, but as we've explored, its influence permeates multiple levels.
An efficient dock scheduling platform goes further than coordinating inbound and outbound loads. It’s a safeguard of inventory accuracy, a driver of cost savings and speed, and offers a transformative level of visibility and control.
As we advance towards an increasingly digitized future, investing in powerful dock scheduling software like DataDocks is not merely an option, it's an essential strategy for staying competitive.