How does your facility rank in the grand scheme of modern shipping and receiving operations? Leading the pack or bringing up the rear?
This guide takes you through the various phases of dock scheduling maturity, highlighting the unique challenges, solutions, and opportunities that each phase presents. Find out how you’re doing compared to North American industry standards, and explore ways to get your loading dock running more efficiently and predictably.
For a practical guide on implementation, check out our introduction to dock scheduling.
1. First-come-first-served
Approximately 15-20% of facilities*, including many smaller e-commerce businesses, high-mix manufacturers, and much of the food processing and preservation industry.
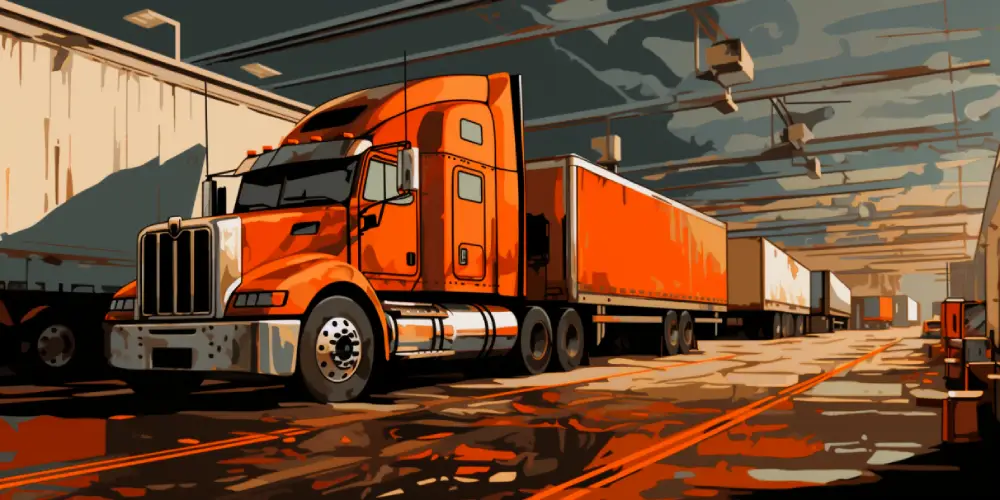
Some operations are hesitant to maintain a schedule for shipping & receiving. Instead, trucks are loaded and unloaded in the order they arrive. If appointments are made, they are basically meaningless. Sometimes they can’t even reliably predict the day a truck will come, much less the hour.
If most of your carriers are independent owner-operators, it can be difficult to move away from FCFS. But when deliveries are consistently delayed or even missed, staff are overwhelmed one minute and idle the next, the yard is always congested or detention fees are piling up, it’s probably time for an upgrade.
The first thing to do is appoint a shipping coordinator or clerk. These responsibilities can be taken on by a supervisor on the floor, but in many cases it’s advisable to hire someone with secretarial experience for the role.
Next, it may be helpful to add signage to direct drivers to the right dock door. You may need to train staff on the new procedures, such as how to identify an incoming load. Of course, a conversation also needs to take place with customers and carriers to let them know your facility will now be operating on an appointments basis.
2. Low-tech Appointment Booking
Around 30-35% of facilities. Common amongst businesses that rely heavily on outsourcing their operations. These organizations typically need to conform to the processes and systems of their logistics partners.
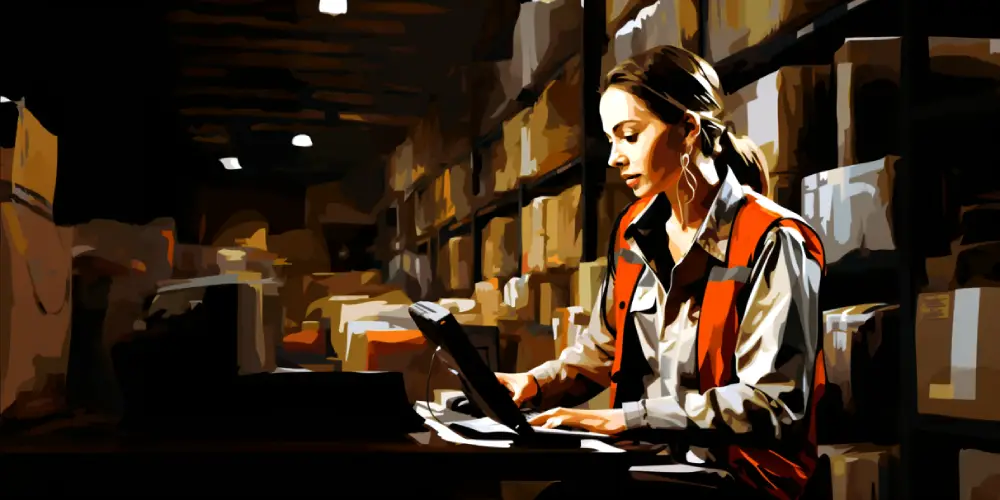
This level of shipping maturity is characterized by the coordinator living in the eye of the storm. They’re constantly mitigating disruptions, which blocks them from being able to drive operational improvement.
Carrier and customer relationships are often shaky, overbookings and errors are likely, and no structured data is being collected, so it’s hard to do process improvement. At this stage, the loading dock is probably the biggest source of frustration for the warehouse manager.
Companies can get stuck here for many different reasons. They might be resistant to change, or lack the resources to invest in improvement.
But more often, the business is in a reactive mode, constantly adjusting to the demands and schedules of carriers instead of actively managing their loading dock operations. This can lead to a vicious cycle where the business avoids conflicts and negotiations due to a fear of rocking the boat.
Moving on from this stage requires frank, sometimes uncomfortable conversations and a shift in mindset. You have to question old assumptions about how fragile certain relationships are, the level of risk involved in change versus interia, the potential advantages for carriers and what an orderly loading dock would really mean for the business.
3. Excel Stretched to its Limits
Approximately 25-30% of facilities. Often seen in medium to large organizations that have grown quickly without investing proportionally in their infrastructure.
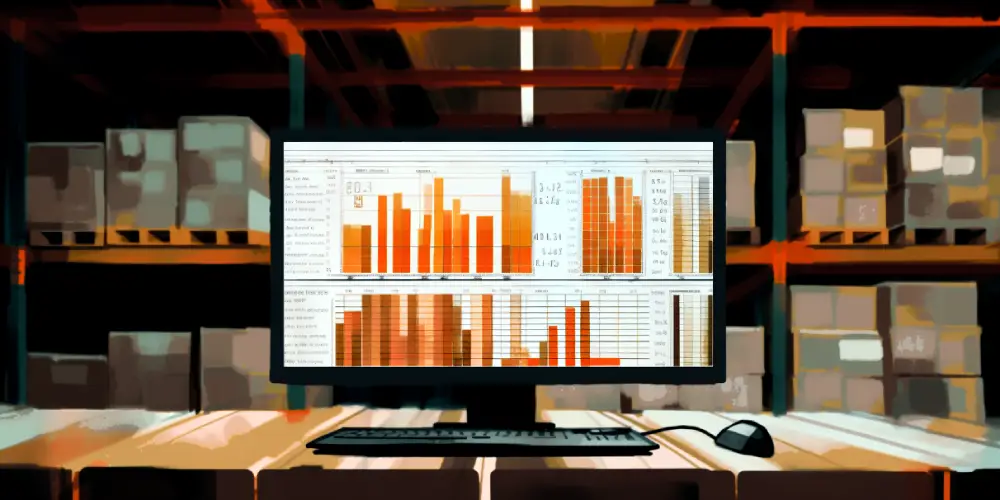
This is where organizations tend to land when they have good people in the loading dock, making the best out of limited technology.
The clerk has a sophisticated spreadsheet-based system for managing the schedule, but is constantly firefighting with back-and-forth emails to carriers and suppliers, and has to manually check P.O. numbers against appointments.
Sometimes there’s a TV screen in the loading dock, but it might be a little hard to read if it’s just showing an Excel sheet.
Companies may perceive the process of adopting new systems as expensive, disruptive, and complex. There's also an apprehension about relinquishing the control that a manual, familiar process provides.
The clearest sign that it’s time to change is when loading dock staff frequently have a hard time identifying a load. “What is this truck?” - mistakes are being made, and although data is certainly being collected, it’s not complete enough to enable real analysis and optimization.
Upgrading from excel to a dedicated dock scheduling platform can actually be relatively painless. The first step is to research the software options that are available today, and start defining some requirements and preferences in terms of features, usability and support. Then arrange demos with whichever vendors seem promising.
Some questions to ask vendors include:
- What does the implementation process look like?
- What kind of training and ongoing support do you provide?
- How does your system handle unauthorized appointment attempts?
- How customizable is the software to suit our specific needs?
- How does your software handle changes or disruptions in schedule?
- Can your software integrate with our existing systems?
4. Still need your phone calls
Around 20-25% of facilities. The norm in many large, older enterprises that began their digital transformation journeys late. While they've started investing in technology, they are hampered by complex legacy processes and systems.
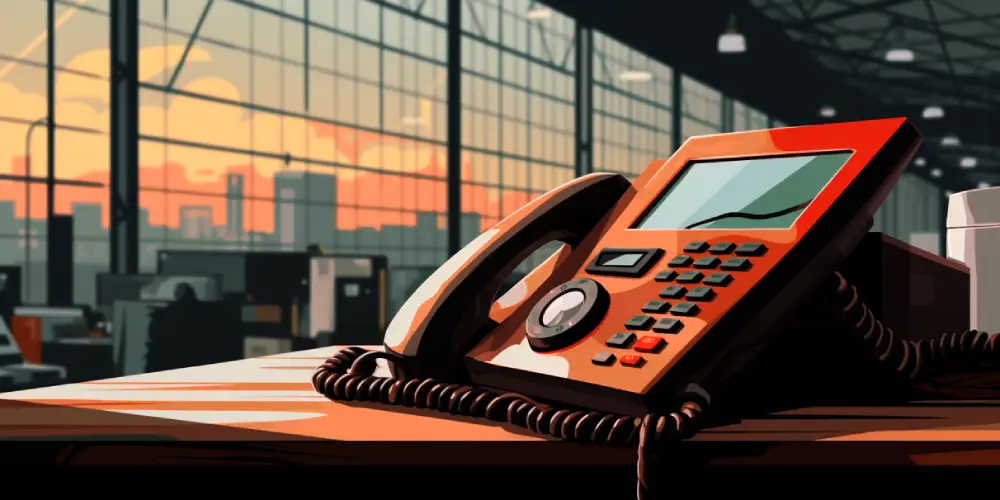
Ideally this is a transitional stage. In the first few weeks of implementing a comprehensive dock scheduling system, some carriers and customers may have lingering doubts, or there might be some additional configuration needed as staff get acquainted with the new system.
However, in cases where the software is not exactly fit for purpose, this phase can be sticky. This happens very frequently when the ‘dock scheduling’ system is a small module of a broader WMS or ERP system. These implementations generally lack some of the essential features that make a dedicated dock scheduling system run well.
The challenge with moving on from this stage is correctly identifying whether it’s the software or the process that’s causing the problem.
You can address this with a simple litmus test: if most of your problems are rooted in communication or collaboration issues within your team or with partners, a more advanced dock scheduling system is probably the solution.
5. Automated Dock Scheduling
Roughly 3-5% of facilities. Seen in forward-thinking organizations, especially those that have strategically prioritized their supply chain operations. The standard amongst highly-competitive distributors and flexible 3PLs.
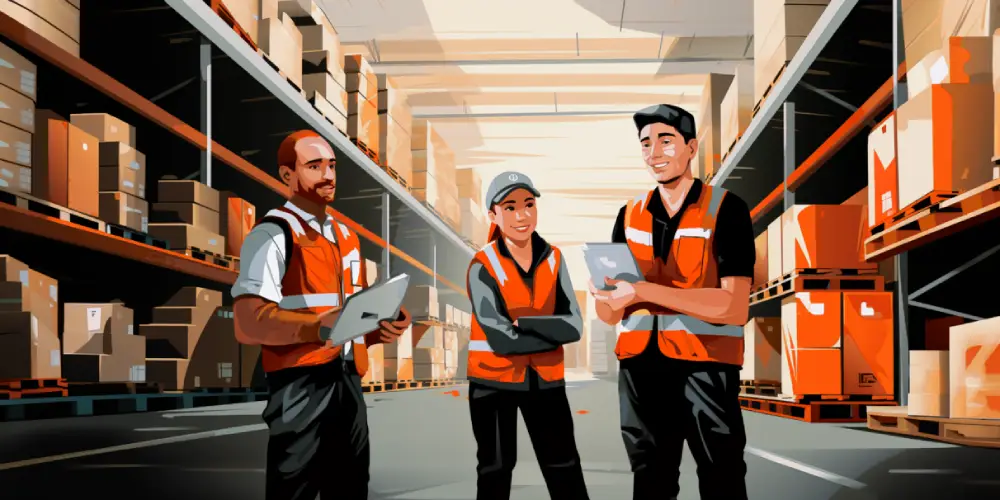
Automated dock scheduling represents a shift from reactive to proactive shipping and receiving operations. This level of maturity is typical for facilities that have been using a comprehensive dock scheduling platform like DataDocks for a few months.
In this new paradigm, managers, no longer held back by firefighting, have more time for long-term process optimization and coaching of staff. The shipping and receiving clerk is also able to plan ahead, predicting peaks in demand and adjusting accordingly.
Labor can be allocated more effectively, reducing idle time and giving staff predictable and balanced workdays, not to mention the chance to get home on time.
Visibility and accountability are other notable benefits of automated scheduling. The system provides clear data that can be used for meaningful conversations with carriers about improving turnaround times. Underperforming carriers can be easily identified, as can patterns like superior performance on certain days of the week.
When disruptions do occur, the schedule can be adapted in real time, automatically notifying all affected parties.
6. Predictive Scheduling & The Future
Less than 1% of facilities. Found at digitally-native companies pursuing a 'vertically integrated' approach, and large-scale enterprises that understood tech and got ahead. Often it’s a single high-performing facility standing out in its organization, pushed forward by internal champions.

At present, predictive scheduling with DataDocks represents the cutting edge of dock scheduling technology. After successfully onboarding the majority of supply chain partners, and customizing the algorithm based on past trends, facilities can make highly accurate predictions about arrival and departure times, staffing needs, and potential disruptions.
The next frontier of dock scheduling technology will likely involve more artificial intelligence (AI), so that predictions can be improved over time without the need for manual intervention.
Another future possibility is even deeper integration of predictive scheduling with other operational systems, creating a truly interconnected, intelligent, and visible supply chain. This could open up enormous improvements in purchasing and inventory management, not to mention enabling precise real-time updates for customers.
Finally, predictive scheduling could be combined with Internet of Things (IoT) technology to create a fully integrated, real-time tracking and monitoring system. Combined with GPS data to track the position of carriers, this data could feed directly into the scheduling system, allowing for even more accurate predictions and real-time adjustments.
Need Help Upgrading your Shipping and Receiving?
Whatever stage you’re at now, the DataDocks team is ready to give you a free consultation and help you modernize your operations.
For some organizations the best approach is to go step-by-step, using technology to simplify workflows and make everyone’s lives easier, and leaving plenty of time for the team to get used to it. In other cases, you can leapfrog to a high level of digital maturity in a short amount of time. Every case is different.