These days, warehouses are expected to do more with less.
A big part of that is cost-cutting, but it’s also getting harder and harder to hire experienced warehouse workers.
Warehouse managers have to rethink traditional methods and adopt innovative strategies to maintain productivity. It's about making every element of our operations smarter, from optimizing every square foot of warehouse space to ensuring each team member's efforts are maximized. The catch 22 is that it's harder to run thorough warehouse audits with a small staff, but knowing where to optimize is crucial to making operations work.
Our game plan will be:
- Weeding out the processes that don't contribute to our KPIs.
- Leveraging data to anticipate demand and plan accordingly.
- Building a team of multi-skilled employees ready to step into different roles as needed.
- Using technology to multiply the productivity of our existing workforce.
Since throwing more bodies at the problem isn't an option anymore, the focus must shift towards implementing workable solutions that address the core challenges faced in the trenches of warehouse management.
That’s exactly what we’ll address in this blog.
4 Core Challenges of Managing Warehouse Personnel
What happens in the warehouse directly impacts customer satisfaction and the bottom line.
So, you need to be aware and be ready for the challenges you’ll face when you work with your warehouse personnel.
High turnover rates
Your warehouse personnel are the bread and butter of your operations.
When you have a shortage of experienced warehouse staff, sooner or later, you’ll have painful problems to deal with—like incomplete inventory, missing goods, and furious customers.
One of the main reasons for high turnover rates in the logistics industry is a lack of confidence in the future. A lot of warehouse workers also say they are treated disrespectfully on the job, while others point to a lack of clear feedback.
As a result of these high turnover rates, the logistics industry is ever more dependent on temporary staffing agencies. Additionally, the baby boomers are retiring, and there are not enough people to replace them.
So, your warehouse company must become more desirable to potential employees by offering better opportunities for advancement or giving powerful incentives so they want to stick around.
Maintaining productivity
Things can sometimes get very tiring and boring in the warehouse due to the repetitive nature of warehouse labor. Your warehouse personnel feel this the most.
As a result, they often lack motivation, and their productivity decreases. This can be a problem if it goes on. Your efficiency takes a hit, leads to more bottlenecks, and can ripple throughout your warehouse operations.
Safety concerns
As a warehouse manager, you are responsible for selecting, acquiring, implementing, and maintaining both hardware and software. This includes ensuring that tools like forklifts and warehouse management systems are fit for purpose.
Plus, you also have to follow legal obligations, while implementing rigorous safety protocols to prevent workplace injuries. Depending on the industry, this may include managing cold chain requirements, maintaining a transparent audit, conducting regular safety drills, and addressing any hazards immediately to prevent accidents.
Communication barriers
As a warehouse manager, you will deal with different types of warehouse employees.
And a lot of times, different types of people have different opinions, concerns, and ways of communicating. So, you should think of ways to have effective communication and a positive work environment to maintain productivity and a smooth-running business.
How to Run a Warehouse: Key Strategies for Managing Employees
Now that we have a clear idea of the problems you’ll face with your warehouse employees, let’s talk solutions.
Refine your hiring and onboarding process
If you just hire people without a robust process, you’re basically hiring without standards and setting yourself up for a messy warehouse.
To optimize your hiring and onboarding process, start by thinking about the roles you need to fill. Do you need more pickers? More forklift operators? Or maybe more people who will maintain the equipment?
Re-check your warehouse operations to see where you’re lagging. You can even ask your current employees what aspects they need more help with.
Then, figure out how many people you actually need. Factor in the following:
- Size of your warehouse
- The volume of orders
- Technologies you use (as it usually reduces the amount of workers needed).
This is to avoid overstaffing and understaffing. If you overstaff, it can lead to more costs and warehouse congestion. But if you understaff, you won’t be as efficient as you can be.
Once you figure out your needs, always try to conduct proper 1-on-1 interviews in your hiring process to see your potential employee's character and their bigger vision. It also sets the foundation for a great work relationship. This way, you can truly find someone who’s an A-player and you’ll know how to support them better.
Remember not to rush through the hiring—even if things get hectic. Always be intentional with your approach as it often results in a more resilient team, lower turnover, and heightened productivity.
Figure out how you can package a great offer
Before even thinking about “hiring the right people,” you must be the right company for these people. Ask yourself, “What can you offer them that other warehouses can’t?”
When you take the steps to make the job’s rewards outweigh the challenges, more experts, disciplined, and motivated people will follow.
Raising the pay might be the first thing that comes to mind (it would be good if you could). But think outside the box. Instead of just pay increases, you can package it with things like:
- Getting home on time: Lots of warehouses can’t offer this because of fluctuating workloads. When you offer this, you’ll get a lot of workers who will prefer working with you.
- Proper ventilation and fans: A warehouse can get too hot, too cold, or too dusty. This is one of the reasons why many warehouse workers leave. They feel drained and uncomfortable, all while doing a physically demanding labor.
- A relaxing breakroom: Warehouse workers will typically get 15-60 minute breaks, so make it worth their while. Don’t let them just sit on a stack of pallets. Do your best to give them comfortable seating, a microwave, coffee machine, fridge, free drinks, or good Wi-Fi so they can really recharge and relax.
Hire people who can take the job’s demands
You can find people like these by setting clear expectations from the start and respecting potential employees by being honest with the nature of the work. Let them know from the start the challenges and rewards they’ll get from being a warehouse worker.
Also, try to advertise in places that have great prospects for warehouse labor demands.
For example:
- Advertise in veteran groups because veterans are used to discipline, hard work, and pressure. Give them fair work, honest pay, and a team that values them—you’ll see the lengths they’ll go to.
- Or gyms, where many people are already used to physical work and love getting their exercise in. They might love a job that helps them maintain their strength and fitness levels while earning a living.
Improve team communication and relationships
Warehouse employees don’t like being left out in the dark. They are already tired from all the lifting and moving heavy packages. If you suddenly change their shifts without them knowing, you might as well expect them to leave.
Make sure that important changes like these are communicated consistently to your team through meetings. When arranging a meeting with your team, find a balance between team meetings and 1-on-1 conversations.
The team meetings are for general announcements. However, only hold team meetings when you’re going to relay necessary information. Don’t just do meetings for the sake of meeting. If there are announcements that don’t need to be told personally, save yourself and your employees the time.
You can simply create a group chat with all your employees where you only announce important stuff. If you can, have separate group chats for different warehouse roles (e.g., forklift operators, pickers, team leaders) to relay specific information for the role.
They would appreciate the time you save them as they can get more time for their personal stuff.
The 1-on-1s are for more personal input. A great idea for this is to hold it once every month or three months. You wouldn’t want situations where your employees are already tired from work and you still ask them to have a long talk with you.
When talking about your employees personally, ask them about things you can help them with, their issues, and some feedback in the warehouse. However, respect their privacy. Only let them share what they want to share.
For an added touch, you can also plan team getaways so they can bond with their co-workers outside of work. This lets them relax and have some fun with their co-workers outside of the warehouse.
Training and development
Additional knowledge and skills are some of the most valuable things supply chain businesses can give to their employees. Because most of them only consider warehouse work as stepping stones, not lifelong careers.
There are even Reddit threads that talk about their stories where they start as a warehouse worker and move up in the corporate world—stories like people starting from warehouse work, to getting a degree in supply chain business to be a business buyer.
You need to take this fact and use it to your advantage to make your company more attractive to potential employees.
Here are some strategies you can use:
- Outline clear steps from entry-level to advanced positions. For example: Picker/Packer → Inventory Specialist → Team Leader → Warehouse Manager. This will help you choose the specific list of skills to develop for different employees.
- Pair new hires with experienced workers. Rotate employees through different tasks to build skilled teams. Let them assist supervisors in scheduling, tracking shipments, or handling inventory.
- Teach them the skills they can use for their future and in the warehouse. Skills like leadership, quality control, equipment maintenance, or using warehouse management software can help them be more capable as they plan to change careers. If you can offer them certificates, much better. They will have tangible proof they learned the skills.
- Reward them with pay and perks. Employees won’t commit to training unless they see real benefits. You can offer tiered wage increases based on skills learned (e.g., a $0.50/hr raise for completing a leadership course). You can also give one-time bonuses for earning certifications.
Even though most warehouse employees wouldn’t stay, you’ll be more attractive to other prospective employees when you offer training and development. You’ll have a larger pool of people with experience and work ethic.
Focus on “process improvement” tracking, not tracking your people
Tracking your warehouse employees’ every move with software and connected devices to measure their performance might seem to get results—especially for big companies like Amazon.
That’s because they can be relatively confident that even if workers quit frequently, new hires can quickly adapt and meet performance standards due to strict monitoring and predefined workflows.
But trying to copy this comes with disadvantages:
- A recent study found that employees under surveillance were more likely to take unauthorized breaks, ignore instructions, damage company property, steal office supplies, and intentionally reduce their work speed.
- Research from the EU indicated that monitoring employees through automated systems, software, or machines increases psychological risk factors. The study also revealed that while data-driven technology enhances performance, businesses that used analytics to improve processes performed significantly better than those that focused solely on monitoring employees, without the negative impact on worker well-being.
- A California Law Review paper argued that while employers have a legitimate interest in productivity and preventing misconduct, this should not come at the expense of workers' privacy and personal freedom.
So rather than just copying companies like Amazon, use data analytics for process improvement rather than tracking your people.
Focus on things like:
- Improving your order fulfillment speed & reducing shipping delays: Monitor data like average order processing time per product type, shipping accuracy rates (on-time vs. late deliveries), and identify delays in packing, scanning, or loading onto trucks.
- Minimizing machine downtime: Track usage hours of forklifts, conveyors, packing machines, etc. Then, try to analyze when equipment is likely to fail by logging the frequency of equipment breakdowns.
- Identifying bottlenecks & slowdowns in the warehouse: Try using heatmaps to track high-traffic areas that cause congestion or identify frequent rework areas (e.g., mispicked items, repacking zones).
Focusing on tracking the process improvement rather than just tracking your people gives you a more tangible and clear pathway to positive change.
How to Run a Warehouse with a Reduced Headcount
The following strategies are designed to optimize operations and foster a culture of continuous improvement. These approaches will guide managers through the practical steps necessary for maintaining productivity and efficiency, even when resources are constrained.
Eliminating Non-Value-Added Activities
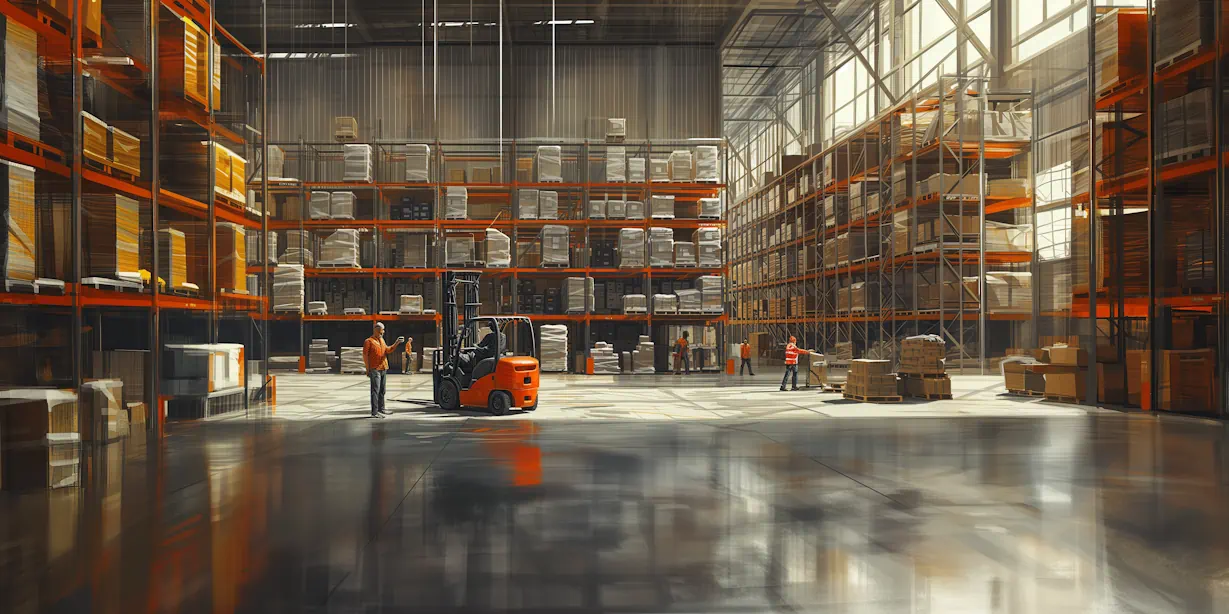
In the hustle of daily warehouse operations, it's easy for non-value-added activities to creep in. These are the tasks that consume time, space, and resources but don't directly contribute to customer satisfaction or the bottom line.
The lean methodology encourages us to look critically at our processes and ask whether each step adds value. Identifying and eliminating these activities can significantly streamline operations, particularly when you're operating with a stripped-back workforce.
Step 1: Identify What Doesn't Add Value
Start by mapping out each step of your operations, from receiving to shipping. Involve your team in this review; they're the ones on the ground every day and can provide insights into which tasks feel redundant.
Receiving is a good place to start. You can read our in-depth guide to optimizing this process here.
Common Culprits:
- Excessive Movement: If your team is walking back and forth across the warehouse for items that are frequently used together but stored separately, you're looking at wasted time.
- Over-processing: Doing more to a product than what is required by the customer or next process step, like overpacking items, is a common non-value-added activity.
- Waiting: Anytime goods are sitting idle, waiting for the next step in the process, you're facing inefficiencies. This could be due to machine downtime, waiting for approvals, or bottlenecked operations.
The philosophy of Total Quality Management (TQM) emphasizes the importance of customer satisfaction and process improvement, suggesting that reducing waiting times and over-processing directly contributes to a higher quality output and customer satisfaction.
Step 2: Streamline and Simplify
Once you've identified these non-value-added activities, it's time to take action. Here are a few strategies:
- Reorganize for Efficiency: Look at your warehouse layout. Can you minimize movement by rearranging storage? Often, placing items that are frequently used together in closer proximity can save a lot of time.
- Review Your Processes: Challenge every step of your process to ensure it's necessary. Simplify where you can. If there's paperwork that can be digitized or steps that can be combined, make those changes.
- Address Bottlenecks: Identify where delays typically happen and find solutions. This might mean upgrading equipment, retraining staff on certain processes, or changing the way tasks are scheduled.
Addressing bottlenecks is a key aspect of the Theory of Constraints, which focuses on identifying the most significant limiting factor that stands in the way of achieving a goal and systematically improving that constraint until it is no longer the limiting factor.
Step 3: Continuous Improvement
Eliminating non-value-added activities is an ongoing commitment. Encourage your team to always be on the lookout for inefficiencies and to feel empowered to suggest improvements. Regularly review your processes and adapt as necessary. The goal is to create a culture of continuous improvement where everyone is aligned on making operations as lean and efficient as possible.
By tackling non-value-added activities head-on, you're not just cutting costs; you're improving your team's ability to deliver quality service quickly. In a competitive landscape, these efficiencies can be the difference between just keeping up and truly excelling.
Demand Planning and Dynamic Slot Allocation
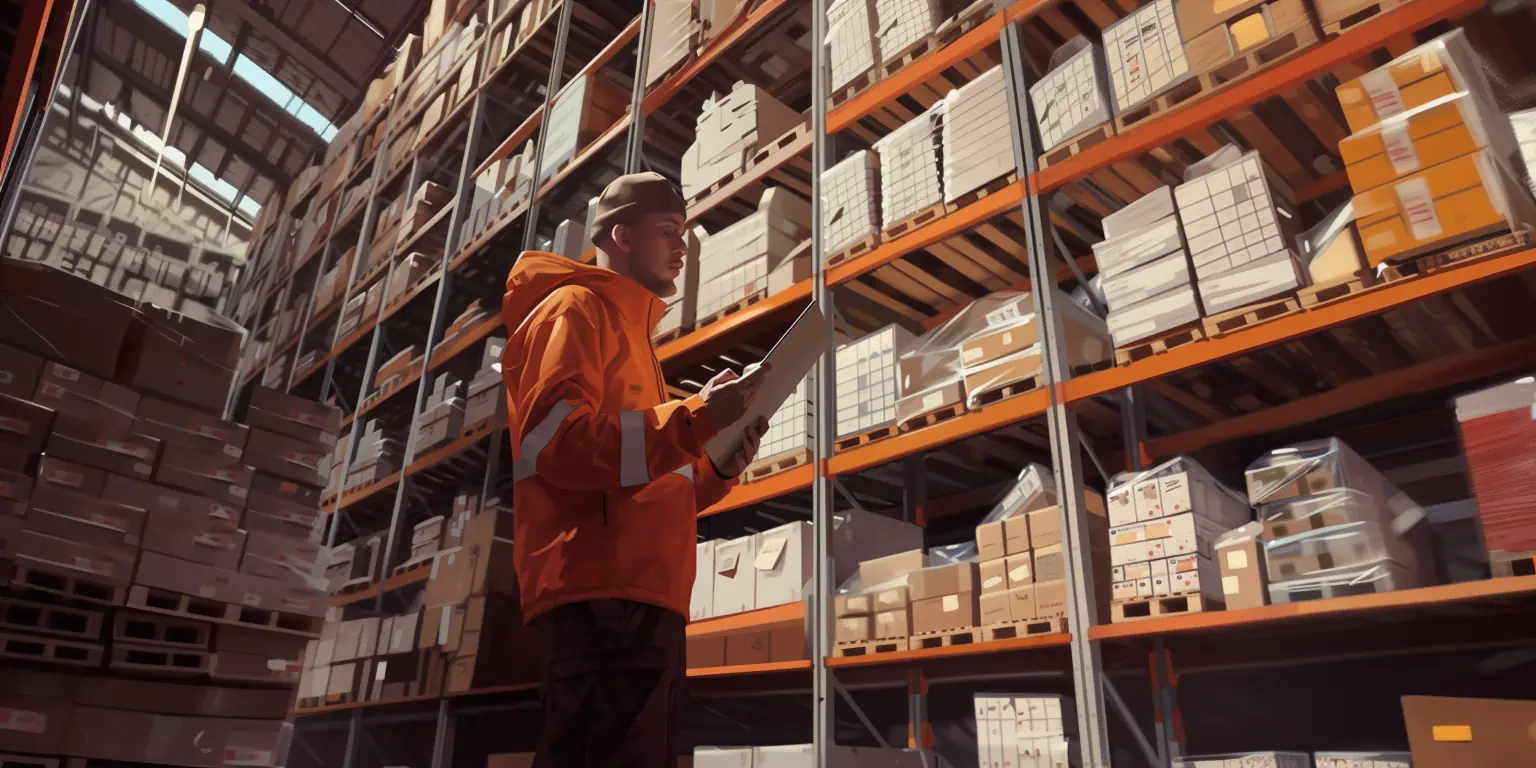
Data-driven warehouse operations harness the power of analytics to streamline every aspect of their processes, from inventory management to order fulfillment.
Even warehouses with simple information systems can get a lot of mileage out of forecasting demand based on historical data. Plenty of warehouses use this to guide their replenishment strategy, but few take it to the logical next step: dynamic slotting.
Dynamic slotting moves beyond traditional static models that often lead to inefficiencies, such as the unnecessary movement of slow-moving items or the need to periodically overhaul the warehouse layout in response to seasonal changes.
By continuously updating the layout of the forward area, dynamic slotting ensures that the most in-demand items are always stored in the most accessible locations. This approach eliminates the need for large-scale movements of goods and allows warehouses to respond to demand fluctuations without additional labor.
For instance, rather than adhering to a fixed set of SKUs in the forward area for extended periods, dynamic slotting adapts to order fluctuations over time. This adaptability is particularly crucial when unexpected high-order quantities arise, making it more efficient to pick certain items from the reserve area rather than the forward area.
By replenishing empty slots with the correct products as needed, without any unnecessary moves, warehouses can maintain optimal efficiency and service levels, even when operating with fewer staff.
This strategy shines in environments where demand patterns are unpredictable. The ability to swiftly adapt the warehouse layout to changing demands—without relying on manual intervention or extensive planning—ensures that workers spend less time navigating the warehouse for items. As a result, the warehouse becomes more efficient, reducing its reliance on a large workforce to manage fluctuations in demand.
Incorporating a dynamic slotting approach allows warehouses to leverage data and analytics fully, transforming operations to be more agile and responsive. By focusing on high-impact strategies like dynamic slotting, warehouses can achieve significant operational improvements, even with a leaner team.
Workforce Flexibility and Cross-Training Core Employees
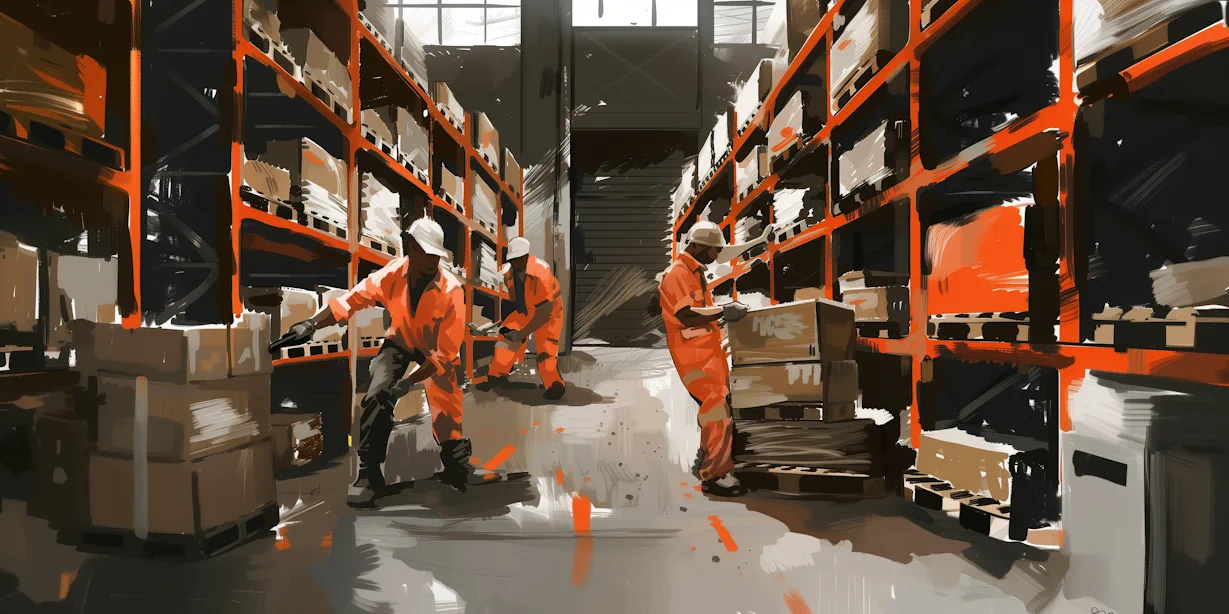
If demand forecasting is a cornerstone of effective warehouse operations with a reduced headcount, forecasting errors pose a significant challenge.
Workforce flexibility serves as a crucial buffer that allows organizations to adapt swiftly to changes and maintain efficiency despite inaccuracies in demand predictions.
There are two main strategies for enhancing workforce flexibility: the integration of part-time labor and the implementation of cross-training programs.
One way to go about this is to build relationships with staffing agencies or develop a pool of trained part-time workers who can be brought in quickly to manage workload peaks without the need for permanent headcount increases. This scalability is particularly valuable in managing unexpected demand surges or drops in demand, ensuring that needs can be met without compromising service levels or incurring unnecessary costs.
But cross-training core employees is also essential. This strategy not only diversifies the skill set within your team, making your operations more flexible and resilient to fluctuations in demand but also significantly enhances problem-solving capabilities across different functions of the warehouse.
By implementing cross-training, you can build a stronger, more cohesive team ready to tackle challenges collaboratively, ensuring productivity remains high even with fewer hands on deck.
Furthermore, cross-training enables shorter lead times and more reliable delivery by reducing both the mean and variance of cycle times. This reduction is achieved by increasing worker flexibility, which in turn reduces congestion and facilitates smoother operational flows. In warehouses operating with a reduced headcount, this ability to quickly adapt and reallocate resources to meet changing demands is invaluable.
Implementing Technology that Multiplies the Impact of Team Members
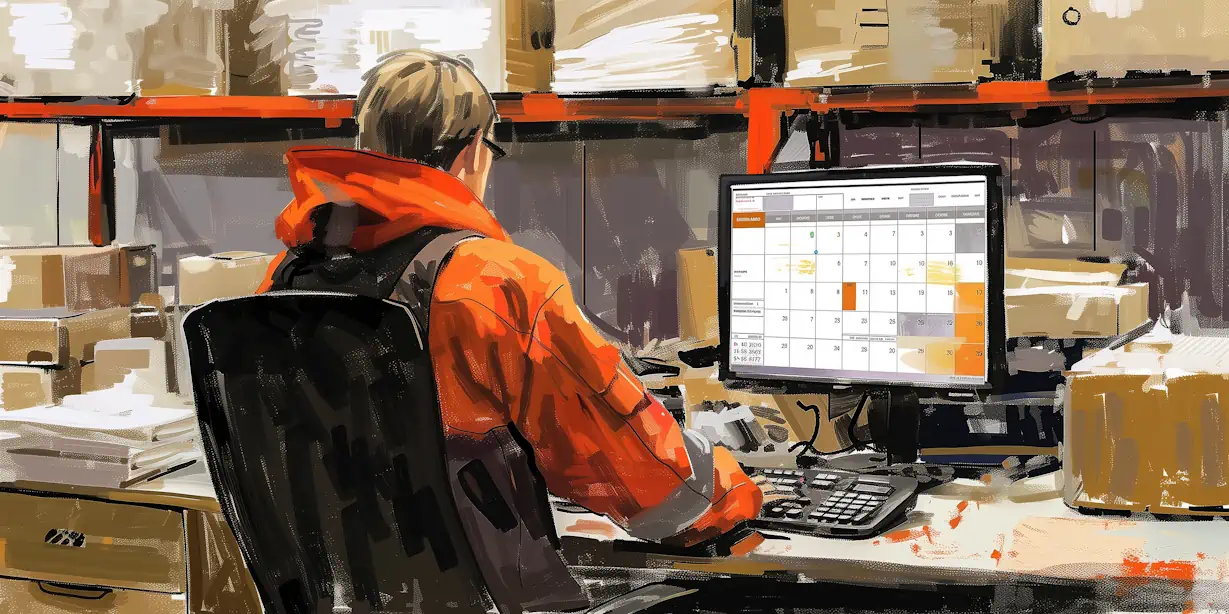
Cross-training workers on different material handling processes can make your operations more flexible and resilient. But that’s only the first step.
With the right technology, you can also empower each member of your team to undertake more complex responsibilities.
For instance, minimizing repetitive administrative tasks enables clerical employees to delve into inventory management or master aspects of the Warehouse Management System, depending on their skills and interests.
Implementing RFID scanning can be a game-changer, automating the tracking of inventory and freeing up employees to focus on more strategic tasks. But the adoption of such technology can also be complex and risky, and there’s already talk of RFID becoming obsolete in the face of more advanced solutions.
Another avenue is dock scheduling.
Dock scheduling software optimizes the loading and unloading process, reducing idle times and increasing throughput without the need for additional labor. This technology not only enhances efficiency but also transforms roles and responsibilities.
One of the most immediate benefits is the elimination of repetitive, resource-draining tasks such as verifying load details. The software ensures that all parties have access to the same information, reducing confusion and enabling workers to prepare for and process each load efficiently.
Dock scheduling is a practical and accessible entry point for workers to start interfacing directly with information systems. Unlike technology that requires extensive training or investment in wearable devices, dock scheduling software is intuitive and designed for the warehouse environment. This ease of use encourages adoption and minimizes resistance, making it an ideal first step for warehouses looking to digitize their operations without overwhelming their workforce.
Loading dock workers can take on responsibility for inspection and documentation, allowing for a more streamlined process where workers are directly engaged with the quality and compliance of incoming and outgoing goods. By integrating these tasks, the need for back-and-forth communication is reduced, minimizing delays.
The role of the shipping and receiving coordinator is also fundamentally transformed by dock scheduling software. Instead of being bogged down with back-and-forth phone calls and emails with carriers, coordinators can now focus on optimizing the flow of goods in and out of the warehouse. They become efficiency experts, using the software's insights to adjust schedules dynamically, reduce bottlenecks, and ensure that the docks operate at peak capacity.
Since the software tracks the time taken to work each load, managers can analyze performance, identify areas for improvement, and implement changes based on real data. This level of oversight encourages a culture of accountability, where every member of the team is aware of their contribution to the operation's success and is motivated to improve.
Dock scheduling is indispensable for warehouses aiming to increase productivity with a reduced headcount. By transforming roles, eliminating inefficiencies, and fostering a culture of continuous improvement, dock scheduling software is a valuable tool in the modern warehouse's quest for operational excellence.
To learn more about how dock scheduling can help you streamline your warehouse operations, give the DataDocks team a call at (+1) 647 848-8250, or book a demo.