Have the Steps of the Warehouse Receiving Process Changed?
Put simply, dealing with inbound loads involves these steps:
1. Check The Purchase Order
Know what’s in the load. Check your purchase order and make sure you’re certain of what to expect from the delivery. This should be done in advance to avoid receiving the wrong goods. You want to ensure that you have the right products and the correct amounts so that nothing is missed or overlooked.
2. Carrier Communication and Arrival
Communicate with the carrier and agree on a time of arrival so that you can accurately prepare the warehouse and everyone involved in the receiving process.
Be prepared that late and early arrivals happen and that the times given are usually estimates due to traffic and the state of the roads.
3. Perform the Initial Inspection
The initial inspection should not be glossed over. It should be as thorough as possible because this is the best time to catch anything wrong with the order.
You don’t want to unload the stock only to find out later that you’re missing products or something is damaged.
4. Focus on Unloading
Unloading should be a methodical process that everyone involved understands. It should be like a well-oiled machine.
The quicker and more efficient the unloading process, the easier the receiving process will be.
5. Further Inspection and Counting
This crucial step is when you ensure that every single product has been delivered and is at a standard you’re willing to sign off on.
You cannot skip this step. Any missing or excess items need to be reported.
6. Putaway or Processing
At this stage, you’ve done all your checks, and you know you have the correct inventory. Now, you need to put it away or, if you're crossdocking, process it for outbound.
Don’t rush this process. Ensure everything is done according to the book, or you’ll regret it later.
7. Issue Resolution
Finally, if any issues came up in any of the checks, now is the time to resolve them. Make a list and ensure each query is addressed.
You don’t want to end up missing an issue and leaving it until it’s too late to resolve and you’re stuck with the incorrect inventory.
A more thorough version of this step would be carrying out a full warehouse audit.
The Impact of Technology
Of course the specifics greatly differ between facilities.
Before modern IT, purchase orders were generated manually and faxed or mailed. Today many companies fully automate this step, even triggering orders automatically when inventory dips.
Communication between warehouses and carriers varies widely. Sometimes, load contents and arrival time information is shared via phone or email, requiring manual data entry. More sophisticated operations use software for real-time data exchange.
The physical tasks of assigning trucks to dock doors, managing traffic and securing vehicles has also evolved since the 1980s. Traffic patterns are more systematic. Communication has shifted from hand signals and two-way radios to traffic lights and, more recently, to mobile notifications.
Stricter regulations have brought in tools like wheel chocks and dock bumpers. Dock levelers, which bridge the gap between the dock and the truck, have become more reliable with hydraulic and air-powered mechanisms.
In the 90s and early 2000s, there was a trend towards conducting a formal initial inspection in the presence of the driver. But as time constraints have become tighter, inspections are increasingly rushed or carried out only after the truck has departed.
Unloading itself has perhaps changed the least, although it can be said that the practice of recruiting the driver as an extra pair of hands has finally disappeared, at least in North America and Western Europe. Manual lifting itself is close to extinction, as forklifts and pallet jacks have become cheaper and pallets themselves more standardized.
The introduction of just-in-time logistics, along with practices such as blind receiving and cross-docking have also changed the industry. Technology plays an increasingly central role, with sophisticated WMS software, RFID or barcode scanners, and of course - dock scheduling.
How Constraints Shape the Warehouse Receiving Process Flow
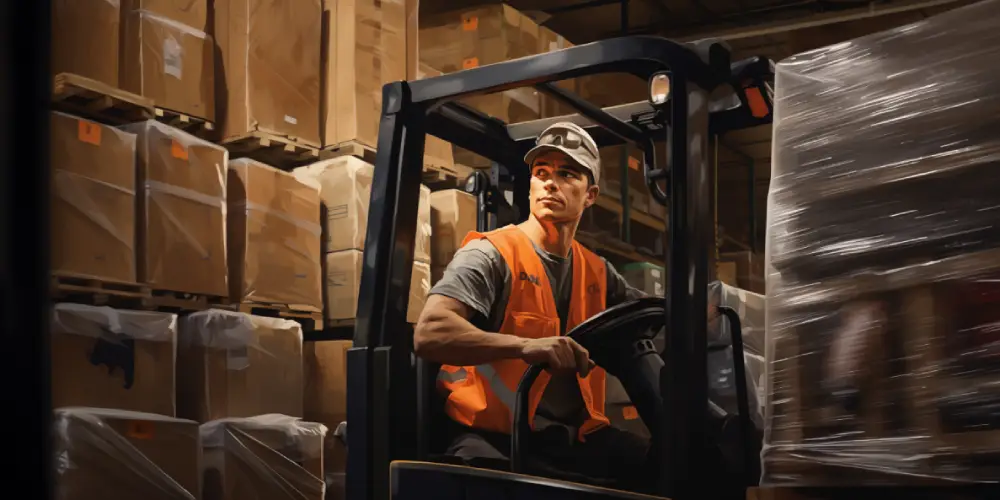
Warehouse operations are dictated by two vital resources: space and time. These intertwined elements shape every process, but none more so than receiving.
The warehouse's physical attributes — size, shape, layout, and dock door placement — greatly impact goods flow. Layouts requiring large distances between receiving docks and storage areas consume more time to move goods.
Dock door placement significantly affects efficiency. In a straight "flow through" layout with inbound and outbound docks on opposite sides, storage rows are usually perpendicular to the doors, facilitating direct goods flow. Alternatively, a "U-shaped" design situates all doors on one wall, where inventory storage arrangements depend on operational needs.
The size of the receiving area directly impacts what actions can be taken after goods are unloaded. With more space, you have the opportunity to conduct pre-sorting or thorough inspections in the staging area, especially if the incoming goods are known to be problematic.
However, if the area is smaller, these operations are more difficult. Mobile workstation carts can alleviate space limitations, but, if the incoming goods are mostly problem-free, eliminating staging in favor of direct putaway might be the best option.
The timing of loads is also important. Warehouses must strive for improved collaboration with suppliers to distribute receipts more evenly across a shift, mitigating congestion and workload spikes. It's crucial to understand that this effort requires negotiation, and success relies on building cooperative relationships with suppliers.
In summary, the intertwined nature of space and time in warehouse operations demands careful decision-making. By striving for adaptable solutions, warehouse managers can facilitate a more efficient and streamlined receiving flow.
Mitigating Risk in Warehouse Receiving Procedures
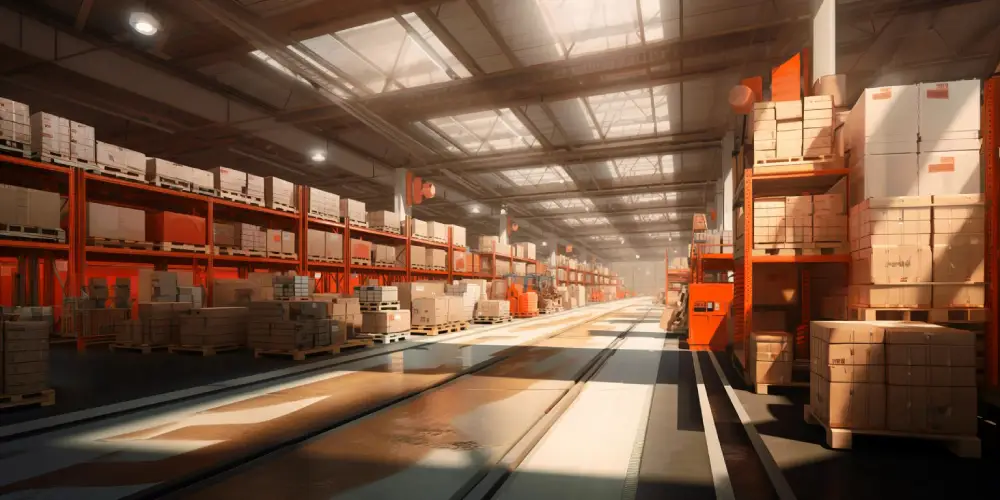
Risk management in receiving is about protecting both the security and integrity of goods, and protecting the time and operational resources of the facility.
The first line of defense is the meticulous checking of goods at the point of receipt. That starts with verifying the integrity of the seal.
A rigorous system for damage identification and handling damaged goods plays an essential role in risk mitigation. Detecting them early protects downstream warehouse processes.
Disruptions can come from multiple sources. Unsolicited goods, incomplete or ill-filled documentation, incorrect quantities, and incorrect labeling can all pose challenges. You can read our complete guide to warehouse challenges here.
The human factor is essential. Many risks originate from incorrect or insufficient staff training or errors in information flow. Ensuring workers are well-trained and informed about the procedures can reduce the chances of such issues. Likewise, accounting for worker fatigue and ensuring proper handling of goods are crucial for maintaining safety and productivity.
Good record-keeping, including the use of receiving checklists, is powerful. Ensuring every case and pallet is labeled correctly, and promptly replacing damaged location tags, helps maintain a smooth and efficient flow of goods.
Lastly, paying attention to general equipment and truck safety maintains a secure environment and reduces the potential for incidents. Regular equipment maintenance and safety checks are integral to this process.
By considering these factors and implementing suitable strategies, warehouse managers can significantly reduce risks in the receiving process.
How Supply Chain Partners Influence the Inventory Receiving Process
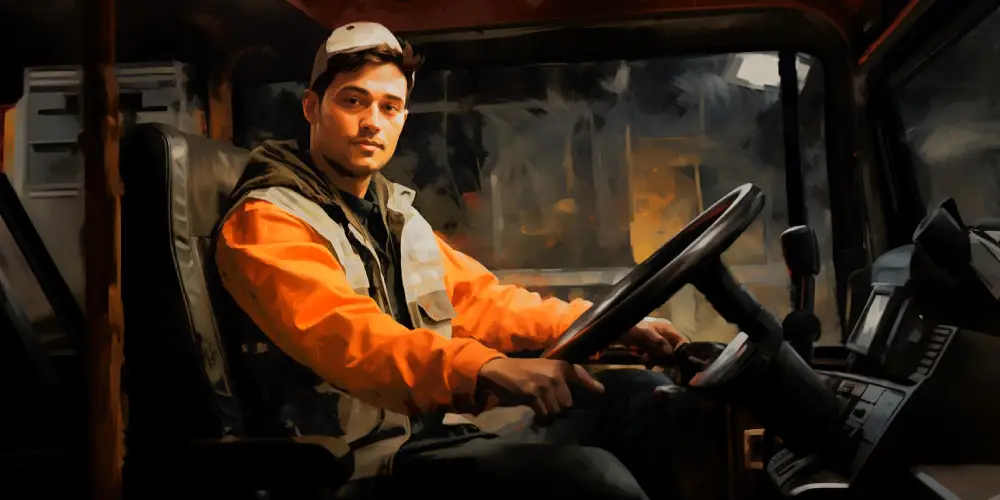
The quality of goods, adherence to packaging standards, delivery reliability, and other factors can greatly influence the efficiency of your warehouse operations.
Reliable vendors' goods can often go directly to storage, saving time and resources. Conversely, loads from certain vendors might need staging due to recurrent issues like product damage or quantity discrepancies.
A vendor ranking system based on reliability can aid in more effective receiving process management. Staff can then anticipate and allocate more resources to shipments from less reliable vendors.
One of the most significant challenges in receiving lies in the lack of knowledge about incoming shipments. Improved coordination with partners can help, as more transparent information sharing ensures better planning and resource allocation.
Setting clear expectations with suppliers regarding packaging, load organization, and documentation can also minimize disruptions.
There are several ways supplier actions can negatively impact your business. They may use inappropriate freight methods or carriers, omit packing lists, ship incorrect or damaged items, or fail to meet delivery deadlines. Frequent occurrences of these issues can harm profitability.
To address this, consider a charge-back program that outlines penalties and remediation steps for non-compliance. Documenting repeat issues and tracking vendor performance can provide the data needed to enforce such a program and bring about improvements.
Successful warehouse receiving depends on supply chain partners' collaboration. Aligning standards, enhancing communication, and holding vendors accountable are key.
Justifying Capital Investments in the Inventory Receiving Process
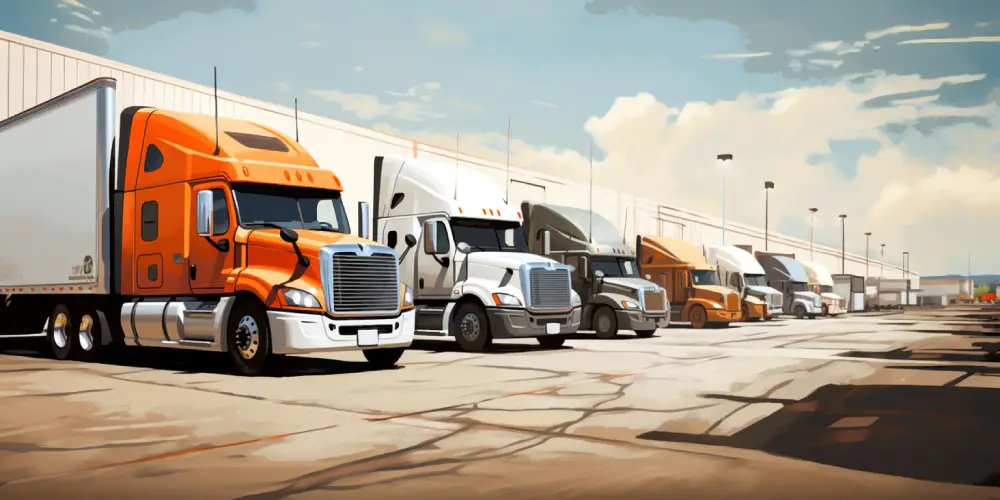
Investing in robust, well-maintained loading dock equipment is a wise yet often overlooked use of capital allocation. High-quality vehicles and tools might have higher initial costs but yield increased efficiency, durability, and lower long-term maintenance costs.
Moreover, smart procurement can yield substantial benefits. Opting for forklifts with wider tires can reduce warehouse floor damage. Automatic dock levelers can adjust for truck height variations, minimizing disruptions during receiving and speeding up operations.
Another area ripe for investment is streamlining the check-in process. Manual check-ins can lead to inefficiencies, like increased detention fees due to long wait times, traffic congestion in the receiving area, and higher CO2 emissions. Use a dock scheduling system to fix this.
Investments in the inventory-receiving process shouldn't be seen as mere expenses. When justified and executed properly, they can enhance operational efficiency, cut costs, and even contribute to sustainability objectives. A thorough evaluation of potential investments can ensure desired return on investment and long-term warehouse operations benefits.
Optimizing Warehouse Receiving Procedures: 5 Possible Strategies
Balancing rigor with speed requires understanding different techniques and their pros and cons.
Implement Blind Receiving
What it is: Blind receiving is a method where the receiving staff is not informed about the exact contents of the shipments they're processing. This encourages a more diligent counting and verification process since workers cannot rely on shipment manifests and must verify each item individually.
Why it works: This method naturally leads to a more thorough inspection process, as workers have no preconceptions about what the shipment contains. It reduces the likelihood of discrepancies between the manifest and actual contents going unnoticed.
When it's appropriate: Best suited for operations where the cost of errors is high, or where there's been a history of discrepancies. It may not be suitable for very high-volume or rapid-turnaround environments due to its time-consuming nature.
How to implement: To implement blind receiving, withhold shipment details from dock workers and provide them only with the information necessary to identify and count the items. Use this strategy selectively for shipments where accuracy is critical or when trying to audit the accuracy of regular processes.
Conduct Pre-Unloading Inspections and Quality Tests
What it is: This strategy involves performing inspections and quality checks before goods are unloaded from the transport vehicle. It ensures that only goods meeting the specified quality standards are accepted into the warehouse.
Why it works: Early detection of non-compliance or defects allows for immediate action, such as rejecting damaged goods or documenting issues for claims, without disrupting the warehouse flow.
When it's appropriate: Particularly useful for shipments from new or historically unreliable suppliers, or for high-value items where the cost of defects is significant. Less critical for trusted suppliers or lower-value goods where rigorous inspections might not be cost-effective.
How to implement: Establish a set of quality criteria and inspection procedures for incoming goods. Train receiving personnel to perform these checks efficiently and document their findings.
Leverage Downstream Metrics for Continuous Improvement
What it is: Utilizing warehouse KPIs to assess the effectiveness of the receiving process and identify areas for improvement.
Why it works: These metrics provide objective data on the impact of receiving practices on overall warehouse operations, allowing managers to pinpoint inefficiencies or errors.
When it's appropriate: Suitable for all operations, but particularly beneficial in environments where continuous improvement is a priority. It requires a commitment to data collection and analysis.
How to implement: Regularly review performance data to identify trends or issues. Implement changes based on data insights and measure the impact of these adjustments on the metrics.
Prioritize Staff Training for Detail-Oriented Receiving
What it is: A focus on comprehensive training programs that equip staff with the knowledge and skills necessary to execute the receiving process with high levels of precision and care. Optimizing your recruitment process can also move the needle.
Why it works: Well-trained employees are more likely to follow procedures correctly, leading to fewer errors and higher quality in the receiving process.
When it's appropriate: A worthwhile approach for almost all warehouses, but especially in those handling diverse or complex inventory, where the risk of errors is higher.
How to implement: Develop detailed training modules that cover all aspects of the receiving process, including the use of technology, inspection techniques, and safety protocols. Regularly update training materials to reflect best practices and new procedures.
Balance Rigor with Speed According to Operational Needs
What it is: Adjusting the level of scrutiny applied during the receiving process based on the nature of the operation, the type of goods, and the reliability of the supplier.
Why it works: Not all shipments require the same level of inspection. By tailoring the approach, warehouses can ensure that resources are allocated efficiently, prioritizing thorough checks for higher-risk shipments while streamlining the process for others.
When it's appropriate: This strategy is applicable in all operations but is particularly valuable in those with a mix of high and low-risk shipments. It allows for flexibility and efficiency, optimizing resource use while maintaining quality standards.
How to implement: Analyze past performance and supplier reliability to develop criteria for categorizing shipments. Implement different receiving protocols based on these categories.
Technology & Labor in the Warehouse Receiving Flow
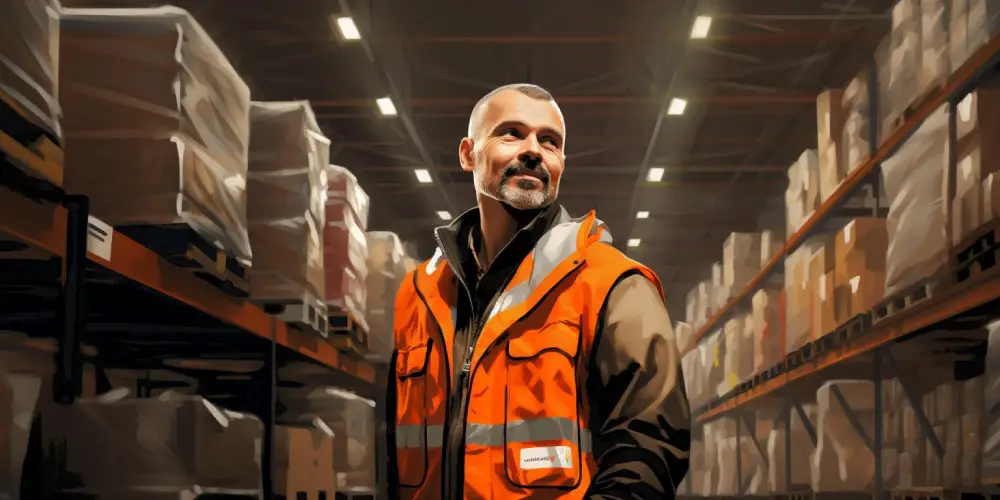
Modern technology and effective labor management are two effective strategies to enhance your warehouse receiving flow.
For instance, barcode scanning for receipts can streamline your operations. But best of all are technologies that facilitate communication between your warehouse and its suppliers or carriers. This could include platforms for sharing real-time updates or automated systems for confirming shipping details.
Another key principle to guide the adoption of technology in warehouse management is the reduction of manual data entry. Not only can this save time, but it also helps minimize the potential for human error. For instance, systems that allow you to bulk upload purchase orders can reduce manual data entry, enhancing the speed and accuracy of inventory updates.
Labor management also plays a vital role. Allocating specific responsibilities helps ensure tasks are carried out meticulously and efficiently. Furthermore, being able to re-allocate staff to areas where they are needed most brings about flexibility, which can prove invaluable in handling unexpected events or peak periods.
Having the right number of man-hours and headcount based on cargo volume and type ensures smooth receiving flow. But this requires accurate inbound load knowledge, emphasizing effective communication with suppliers and carriers. And sometimes you have no choice but to run your operations with a suboptimal headcount.
Successful integration of technology and labor management leads to a more efficient, organized warehouse receiving process. Investment in the right systems and cultivating a flexible, responsibility-focused workforce is sure to boost overall operational performance.